Технология монтажа ротора.
Способы монтажа роторов генераторов зависят от конструктивного исполнения, технологии изготовления, габаритов и блочности поставки их.
Монтаж ротора диаметром до 4 м, поступающего с завода в полностью собранном виде, заключается в наружном осмотре его и установке на место. Для опускания в статор такого ротора необходимо подготовить захватное устройство. Проверка общего состояния ротора и его отдельных деталей заключается в тщательном осмотре крепления полюсов и токопроводов, проверке надежности всех механических соединений элементов ротора и закрепления гаек, определении сопротивления изоляции обмотки ротора. По возможности следует подвергнуть сушке обмотку ротора и произвести электрические испытания ее. После этого ротор закрепляется к крану с помощью захватного устройства и опускается в статор.
Роторы диаметром от 4 до 6,5 м поступают с завода в виде отдельных элементов: остова с втулкой, вала, пакетов сегментов обода, полюсов, тормозных сегментов. Сборка такого ротора при монтаже выполняется в следующем порядке. Остов с втулкой насаживается на вал, собираются пакеты обода и расклиниваются на остове. Затем навешиваются и расклиниваются полюсы, устанавливаются тормозные сегменты, производятся сушка и электрические испытания обмотки ротора, после чего ротор в полностью собранном виде устанавливается на место.
Технология изготовления и блочность поставки роторов диаметром от 6,5 до 7,5 м значительно отличаются от описанных выше. Блоком поставляется только остов ротора, состоящий обычно из двух частей. Все же остальные узлы поступают в виде отдельных элементов: втулки, вала, шихтованных сегментов обода, полюсов, тормозных сегментов. При сборке ротора на монтаже втулка в нагретом состоянии насаживается на вал и фиксируется запорным кольцом. Части остова соединяются между собой и закрепляются на втулке с помощью шпилек. Затем на остове собирается обод из отдельных сегментов, стягивается шпильками и расклинивается. После этого навешиваются и расклиниваются полюсы, устанавливаются тормозные сегменты, производятся сушка и электрические испытания обмоток ротора. Полностью собранный ротор опускается в статор.
Все узлы роторов диаметром свыше 7,5 м поступают на монтаж οι дельными элементами без заводской контрольной сборки. В связи с этим сборка ротора производится полностью на монтажной площадке. Способы и технология оборки таких роторов генераторов подвесного и зонтичного типов существенного различия не имеют. Поэтому ниже будет рассмотрена технология сборки и установки ротора подвесного генератора в качестве основного варианта. Одновременно будут приведены технологические особенности сборки отдельных элементов, а также установки роторов зонтичных генераторов.
Сборка ротора крупного генератора является наиболее трудоемкой и продолжительной монтажной операцией. Поэтому она во избежание задержки монтажа агрегата должна начинаться не менее чем за 30— 40 дней до установки ротора на место и с таким расчетом, чтобы к моменту установки рабочего колеса турбины на место ротор, был уже в основном собран. Технологический процесс поэлементной сборки и установки собранного ротора подвесного генератора может осуществляться в приведенной ниже последовательности:
- кантовка, установка на сборочную тумбу и выверка вала генератора;
- подогрев и насадка втулки ротора на вал;
- сборка, выверка и окончательное крепление остова к втулке;
- установка тормозных сегментов и закладка основания обода;
- укладка и опрессовка сегментов обода;
- дорновка отверстий в ободе для постоянных шпилек, установка и затягивание шпилек;
- дорновка полюсных пазов и навешивание полюсов;
- выверка и расклинивание полюсов;
- расклинивание и выверка обода;
- установка и крепление вентиляторов;
- пайка соединений полюсов и демпферной обмотки;
- сушка ротора, испытания и окраска;
- подготовка и установка траверсы для транспортирования ротора;
- установка ротора в статор на тормозные колодки.
Технология сборки ротора зонтичного генератора с дисковым креплением спид к втулке отличается тем, что вал генератора после посадки на него втулки опускается в кратер агрегата и устанавливается на собранный к этому времени подпятник, опираясь через диок подпятника и сегменты на нижнюю крестовину или опору подпятника на крышке турбины. На монтажной же площадке на выкладках или специальных опорах устанавливается вспомогательная (монтажная) втулка, с помощью которой и производится сборка остова ротора. На вспомогательную втулку устанавливается нижний диск остова, затем ставятся и выверяются спицы остова, после чего на спицы устанавливается верхний диск. Собранный на вспомогательной втулке остов выверяется, и вся дальнейшая сборка ротора производится аналогично сборке ротора подвесного генератора.
Таблица 9-2
Допуски на сборку ротора генератора
меры | Места замеров | Допустимые отклонения, мм, при диаметре ротора (не менее), м | ||
|
| 4,5 | 9,0 | 14,5 |
Концентричность обода | По радиусу до наружного торца спиц (среднее арифметическое от замеров вверху и внизу спицы) | 0,6 | 0,8 | 1,2 |
Концентричность полюсов | По радиусу до внешней плоскости башмака полюса (среднее арифметическое от замеров вверху и внизу полюса) | 0,8 | 1,0. | 1,5 |
Высотное положение полюсов | 5 | 8 | 10 | |
Бой поверхности трения тормозного диска | По плоскости трения диска | 5 | 5 | 5 |
Установка ротора зонтичного генератора такой конструкции на место отличается тем, что в статор он опускается без вала и соединение остова ротора со втулкой производится в кратере агрегата. Опирается установленный ротор на подпятник агрегата, а не на тормозные домкраты.
Если спицы остова ротора зонтичного генератора крепятся к втулке вертикальными плитами, то такой ротор целесообразно собирать на монтажной площадке с валом и в полностью собранном виде устанавливать на место аналогично ротору подвесного генератора.
Допуски на сборку ротора генератора приведены в табл. 9-2.
Установка вала генератора. Во всех конструктивных исполнениях крупных генераторов подвесного типа укрупнительная сборка ротора на монтажной площадке производится вместе с валом и затем полностью собранный ротор опускается в статор.
Рис. 9-9. Насадка втулки ротора на вал.
Валы зонтичных генераторов, как правило, соединяются с остовом ротора через втулку, которая является одновременно и опорной втулкой подпятника. Соединение спиц с втулкой осуществляется двумя дисками либо вертикальными плитами. При дисковом креплении спиц вал с насаженной втулкой устанавливается на место отдельно, а ротор собирается на монтажной площадке с помощью вспомогательной втулки. Собранный ротор опускается на вал, и диски остова соединяются с втулкой. В конструкциях втулки с креплением спиц вертикальными плитами ротор собирается на монтажной площадке вместе с валом.
Насадка втулки ротора на вал (рис. 9) производится в его вертикальном положении на специальной бетонной опоре 1. Отметка верха опоры определяется возможностью подъема втулки над валом при ее насадке. Если ротор собирается на валу, то эта отметка для удобства сборочных работ должна быть такой, чтобы нижняя поверхность ротора располагалась на 700—800 мм выше пола сборочной площадки. На бетонной опоре устанавливается и закрепляется фундаментными болтами монтажная металлическая плита 2 размером несколько больше фланца вала. Количество и диаметр фундаментных болтов должны быть рассчитаны по грузоподъемности крана с тем чтобы они не были вырваны при снятии втулки с вала в случае ее заедания.
До установки вала на монтажную плиту необходимо проверить размеры посадочных мест на валу 3 и во втулке 4. Для этого посадочные диаметры вала замеряются специальной скобой с микрометрической головкой, а внутренние диаметры втулки —микрометрическим штихмассом. Разница замеров вала и втулки даст величину фактического натяга, который может отличаться от проектного не более чем на 10%. Замеры вала и втулки необходимо производить в одинаковых температурных условиях. Должны быть проверены также соответствие и правильность канавки на валу для запорного кольца 5 и шпоночных канавок на валу и втулке.
Для установки на монтажную плиту вал кантуется в вертикальное положение с помощью специального захватного устройства и опускается на место. Поверхность фланца вала предварительно тщательно очищается и покрывается густой смазкой, а на опорную поверхность плиты ставится картонная прокладка. На монтажной плите вал должен быть установлен вертикально с возможным отклонением его верха до 1,0 мм, что проверяется уровнем по торцу вала и регулируется прокладками между фланцем и плитой.
Крепление вала к плите выполняется шпильками. которые должны быть поставлены во все отверстия фланца и равномерно затянуты. Затем на вал надеваются и опускаются на фланец неразъемные детали, расположенные между фланцем и втулкой (выгородка подпятника и др.).
При насадке втулки на вал в горячем состоянии с натягом нагрев ее в зависимости от габаритов втулки и необходимой температуры нагрева может осуществляться мощными электрическими лампами, электрическими печами, элементами сопротивления. Втулки крупных роторов обычно нагреваются с помощью провода, намотанного на поверхность втулки, В процессе нагрева втулка закрывается брезентовым шатром.
Температура нагрева втулки определяется величиной натяга с учетом остывания ее при снятии обмотки, захвате, транспортировке и опускании на вал. Для уверенности в нормальной постановке втулки необходимо, чтобы в момент насадки ее на вал диаметральный зазор между втулкой и валом составлял не менее 1 мм. Практически увеличение диаметра втулки при нагревании с учетом последующего остывания ее должно быть порядка 3—4 мм, а температура нагрева 150— 220° С.
Величина температуры нагрева втулки может быть определена по ранее приведенной формуле (8-2).
По окончании нагревания втулка освобождается от обмотки и стропится к крану с проверкой уровнем вертикальности ее расточки. Перед опусканием на вал проверяется размер посадочного места втулки, после чего может производиться насадка ее; При насадке необходимо следить за направлением шпонки и измерением канавки под запорное кольцо, убедиться в том, что втулка встала на место. В случае, если втулка не дойдет до упорного буртика вала, необходимо снять ее и вновь нагреть до более высокой температуры. Учитывая ответственность насадки втулки, следует тщательно произвести замеры посадочных диаметров и продуманно организовать весь процесс нагрева втулки, захвата, транспортировки и насадки ее на вал.
После насадки втулки вал подвесного генератора остается на месте, и далее продолжается сборка ротора. Вал зонтичного генератора захватывается краном, отсоединяется от монтажной плиты, опускается в кратер агрегата и устанавливается на вращающийся диск смонтированного подпятника. Сегменты подпятника должны быть предварительно выверены в одной горизонтальной плоскости и покрыты слоем густой смазки.
Сборка остова ротора.
Конструктивно остов ротора состоит из лучевых спиц, закрепляемых к втулке или фланцам вала припасованными болтами с помощью верхнего и нижнего дисков либо вертикальных плит, расположенных на втулке и внутреннем торце спиц. Фиксация спиц на втулке осуществляется контрольными штифтами и шпонками. По периферии спицы соединяются между собой распорными балками. Между спицами по наружному концу их устанавливается металлическое листовое перекрытие.
Сборка остова ротора подвесного или зонтичного генератора с креплением спиц к втулке вертикальными плитами (рис. 9-10) осуществляется в следующем порядке. После проверки вертикальности вала, установленного с втулкой на монтажной площадке, к втулке присоединяются припасованными болтами спицы с постановкой горизонтальных шпонок. Наружные концы спиц опираются при этом на металлические тумбы. Спицы выверяются в горизонтальном положении с помощью металлических подкладок между спицами и тумбами и соединяются распорными балками. Затем болты всех спиц плотно и равномерно затягиваются так, чтобы щуп 0,1 мм. не проходил между плитами. Допускаются местные неплотности не более 10% ширины сопрягаемых плит. Общая длина таких неплотных мест в соединении не должна превышать 15% всей длины сопрягаемых плоскостей, а длина отдельных неплотных участков должна быть не более 80 мм. Достаточная плотность сопряжения может быть достигнута применением металлических прокладок.
Рис. 9-10. Сборка ротора подвесного генератора.
1 — монтажная плита; 2 — вал; 3 — втулка; 4 — спица; 5 — шпонка; 6 — штифт; 7 — монтажная опора; 8 — тормозная плита; 9 — домкрат; 10 — опора; 11 — обод; 12 — полюс; 13 — стяжная шпилька; 14 — опрессовочные втулки; 15 — поверочная стрела; 16 — запорное кольцо.
По окончании оборки остова проверяются концентричность его, расстояния между концами спиц, наклон клиновых пазов в радиальном направлении и горизонтальность плоскости укладки сегментов обода, Концентричность обода замеряется вверху и внизу по наружному торцу каждой спицы индикатором или щупом с помощью специальной проверочной стрелы (рис. 9-10). Величины допускаемой неконцентричности обода приведены в табл. 9-2. Расстояния между концами спиц по клиновым пазам могут иметь отклонения в пределах ±1 мм. Выравнивание расстояния между концами спиц может быть в некоторой мере произведено радиальным перемещением распорных балок.
Наклон клиновых лазов в радиальном направлении допускается не более 1 мм на полной высоте паза. Горизонтальность плоскости укладки сегментов обода проверяется нивелированием отметки каждого опорного зуба на торце спицы. Отклонение отметки зуба от средней плоскости допускается в пределах ι±3 мм. При этом за среднюю плоскость удобнее принять отметку самого высокого зуба, тогда на плоскости каждого ниже расположенного зуба можно поставить и приварить подкладки соответствующей толщины. Фиксация собранного и выверенного остова производится постановкой штифтов в плоскостях соединения спиц со втулкой.
При сборке остова ротора подвесного генератора с дисковым креплением спиц на нижний фланец вала устанавливается, расцентровывается по валу и крепится к фланцу болтами нижний диск. На нижний диск устанавливаются, выверяются и закрепляются спицы и затем сверху ставится верхний диск, который крепится к верхнему фланцу вала и спицам. Соединение обоих дисков со спицами вначале производится несколькими временными болтами с фиксацией положения каждой спицы двумя постоянными припасованными шпильками. Остальные постоянные шпильки ставятся и затягиваются одновременно по верхнему и нижнему дискам после закрепления верхнего диска временными болтами. Вся последующая сборка и выверка остова производятся аналогично сборке и выверке остова с креплением плитами.
Сборка остова зонтичного генератора с дисковым креплением спиц (рис. 9-11) производится на вспомогательной втулке, устанавливаемой на монтажной площадке на металлических опорных тумбах высотой 700—800 мм или на деревянных выкладках с металлическими подкладками под втулку. После выверки с помощью подкладок горизонтальности вспомогательной втулки на нее устанавливается и крепится временными болтами нижний диск. Технология дальнейшей сборки и выверки остова подобна технологии сборки и выверки дискового остова подвесного генератора.
Рис. 9-11. Сборка ротора зонтичного генератора.
Сборка обода ротора, состоящего из большого количества (несколько тысяч) отдельных сегментов, является одной из наиболее ответственных и длительных монтажных операций. Поэтому она должна быть тщательно организована и подготовлена. Сегменты необходимо очистить до начала сборки обода от антикоррозийного покрытия, ржавчины и заусенцев, взвесить, распределить по весовым группам и подготовить к укладке. Следует также подготовить монтажные приспособления для опрессовки уложенных сегментов и калибровки (дорновки) отверстий под стягивающие шпильки и пазов для хвостов полюсов.
Очистка сегментов на малоагрегатных станциях производится вручную абразивными кругами и металлическими щетками либо с помощью пневматических машинок со встроенным абразивом и стальной щеткой. На многоагрегатных станциях иногда целесообразно применение специальных высокопроизводительных машин для очистки сегментов, в которых паром и стальными щетками сегменты очищаются от ржавчины и смазки, а механизированными напильниками снимаются заусенцы.
Допустимые отклонения при прокате стального листа и изготовлении сегментов приводят к значительной разнице в весах отдельных сегментов. Поэтому для обеспечения равномерности распределения веса обода по окружности и уменьшения небаланса ротора сборка обода должна выполняться так, чтобы все сегменты одного ряда имели одинаковый вес. С этой целью сегменты после очистки их взвешиваются и раскладываются в пакеты одинакового веса с отклонениями по каждому сегменту не более 0,5 кг. Количество сегментов в каждом пакете должно быть кратным числу сегментов, укладываемых в один ряд. При такой группировке сегментов по пакетам всегда будет обеспечена укладка в один ряд сегментов одинакового веса.
Сборка обода обычно производится с помощью домкратов или металлических тумб. На многоагрегатных станциях для сборки обода применяются в некоторых случаях специальные стенды, на которых выполняется также и опрессовка обода. Первые шесть рядов сегментов обода укладываются с опиранием на зуб спицы и на выверенные горизонтально с точностью до ±0,5 мм тормозные плиты и домкраты. Для фиксирования положения сегментов при укладке в их отверстия устанавливаются не менее трех постоянных шпилек на каждый сегмент, а во все остальные отверстия вставляются временные шпильки. Если сегменты не требуют дорновки, то на место ставятся все постоянные шпильки. Укладывать сегменты каждого ряда необходимо со сдвигом на одно полюсное деление у однохвостовых полюсов и на половину полюсного деления у двуххвостовых полюсов. При укладке сегментов целесообразно уплотнять их по высоте с помощью деревянных трамбовок либо другим способом. Для обеспечения правильной укладки сегментов обода следует составить рабочую схему укладки, в которой должны быть показаны количество сегментов в пакете, высота пакетов и вентиляционных каналов.
Сегменты собранного обода должны плотно прилегать друг к другу, что обеспечивается опрессовкой их в процессе сборки. Опрессовка обода на станциях с небольшим количеством агрегатов производится отдельными пакетами толщиной 400—500 мм затягиванием гаек стяжных шпилек через надставки — втулки разной длины в зависимости от высоты прессуемых пакетов. При опрессовке одновременно с затягиванием гаек сегменты уплотняются ударами медных кувалд или специальным пневматическим молотом. Затягивание гаек производится несколько раз в смену до полного прекращения ослабления их. Во время опрессовки каждого пакета проверяются его высота и концентричность обода.
Пакеты обода должны быть опрессованы до плотного прилегания сегментов.
Допускаются местные неплотности до 0,5 мм только на отдельных и разбросанных по ободу участках. Длина одного или нескольких таких неуплотненных участков, расположенных на одной стороне сегмента, должна быть не более 20% длины этой стороны сегмента. По окончании опрессовки пакет закрепляется в опрессованном состоянии планками, приваренными снаружи обода. После опрессовки всего обода планки срубаются, а места приварки шлифуются. При опрессовке последнего пакета проверяются концентричность и общая высота обода и в случае необходимости меняют число рядов сегментов в этом пакете. Высота опрессованного обода и его отдельных пакетов может иметь отклонение от проектной высоты не свыше 1%. Величина допускаемой неконцентричности приведена в табл. 9-2. Замеры высоты обода и его концентричности производятся с помощью измерительной поворотной стрелы.
На многоагрегатных станциях, где могут быть экономически оправданы дополнительные монтажные затраты, опрессовку обода целесообразно производить в четыре приема нажимными балками с помощью сменных шпилек разной длины, сопрягаемых с анкерными болтами, заложенными в бетонный пол машинного здания (рис. 9-11).
На рис. 9-12 показан примененный в последнее время на монтаже генераторов некоторых крупных гидроэлектростанций специальный опрессовочный стенд, допускающий опрессовку сегментов всего обода независимо от его высоты за один прием. Отличие этого стенда от предыдущего устройства заключается в том, что усилия при опрессовке обода являются внутренними, так же как и в случае опрессовки стяжными шпильками, и на бетон пола здания не передаются. Однако стоимость такого стенда очень велика и его применение может быть экономически оправдано только на строительствах крупных многоагрегатных гидроэлектростанций.
Отверстия под стягивающие шпильки и пазы для хвостов полюсов не всегда полностью совпадают во всех сегментах. Поэтому в таких случаях производится дорновка (калибровка) отверстий и пазов короткими стальными прошивками (дорнами), которые пробиваются через отверстие или паз насквозь ударами пневматического молота по сменной стальной удлинительной оправке, опирающейся на дорн. Дорновка отверстий иод шпильки и полюсных пазов выполняется после опрессовки и затягивания временных шпилек. Для этого последовательно вынимаются временные шпильки, отверстия их дорнуются и затем устанавливаются постоянные шпильки. Дорновка пазов для хвостов полюсов производится также с помощью пневматического молота дорном, имеющим форму паза. Иногда дорновку хвостовых пазов осуществляют с помощью крана машинного здания.
При затягивании постоянных шпилек необходимо следить за равномерностью и величиной напряжений, создаваемых в шпильках. Поэтому затягивание удобно производить пневматическими гайковертами, предварительно выверенными на заданное усилие. После затягивания постоянных шпилек все гайки сверху и снизу обода по одной грани прихватываются электросваркой. От смещения вверх обод фиксируется стопорными планками, установленными на каждой спице и подогнанными индивидуально по месту в зависимости от высоты обода. Затем устанавливаются и закрепляются тормозные плиты, если они не были установлены. Все головки болтов или гайки шпилек, крепящих тормозные плиты, также прихватываются электросваркой.
Собранный обод закрепляется на спицах остова ротора парными клиньями, которые устанавливаются на каждой спице и туго забиваются после опрессовки стали и затягивания шпилек. Одновременно с забивкой клиньев проверяется концентричность обода относительно оси ротора, так как при расклинивании может быть исправлена небольшая неконцентричность обода. Окончательно забивку клиньев обода рекомендуется производить после навешивания полюсов.
При расклинивании клинья забиваются пневмомолотом. Тонкий конец верхнего клина должен дойти до утолщенного конца нижнего клина, который устанавливается заподлицо с нижним пакетом обода. Допускается смещение вверх утолщенного конца нижнего клина, а также тонкого конца забиваемого сверху клина от нижней кромки обода в пределах до 60 мм. Выступающие кверху концы клиньев срубаются.
По окончании сборки и проверки концентричности обода производится проверка средней линии обода ротора — горизонтальной плоскости, проходящей через середину стали обода. Установление средней линии ротора необходимо для правильного навешивания полюсов и определения высотного положения статора генератора, с тем чтобы средние линии ротора и статора в собранном агрегате совпадали. Для определения средней линии ротора с помощью проверочной стрелы замеряются высотное положение верха и низа обода в четырех диаметрально противоположных сечениях и по среднеарифметическому этих замеров наносится риска на проверочной стреле, определяющая среднюю линию ротора. Высотное положение средней линии фиксируется по нижней поверхности фланца вала генератора либо по нижнему диску остова.
Навешивание полюсов.
Изготовленные полюсы не имеют одинакового веса, и разница между весами отдельных полюсов достигает 15%. Вследствие того что балансировка ротора при монтаже является чрезвычайно тяжелой операцией, необходимо избегать ее и принимать все меры к тому, чтобы все детали ротора в процессе сборки распределялись по весу равномерно относительно его оси. Поэтому крайне важно для максимального уменьшения дебаланса ротора, кроме сегментов обода, расположить равномерно по ободу также и полюсы. Выполняется это требование подбором полюсов в четыре группы с минимальной разницей в общих весах групп и последующим равномерным размещением этих групп по окружности обода. Для разбивки полюсов по группам необходимо взвесить каждый полюс, если они не были взвешены на заводе, и выбить на нем вес и номер полюса. Нумеруют полюсы по часовой стрелке, начиная от полюсов с выводами.
Наружная поверхность обода не должна иметь выступающих кромок сегментов, поэтому перед навешиванием полюсов она зачищается. В полюсных пазах обода устанавливают и приваривают опоры для фиксирования каждого полюса по высоте. Проверка высотного положения упоров производится с помощью проверочной стрелы. Середину активной стали накернивают для возможности проверки осевой плоскости установленных полюсов.
После взвешивания полюсы необходимо осмотреть, проверить и испытать на электрическую прочность их изоляцию и полюсы с низкой изоляцией высушить. Сушку полюсов можно производить от внешних источников тока (реостатом, электрическими печами), обдувом сухим горячим воздухом или током.
Перед навешиванием полюсы раскладываются вокруг обода в соответствии с распределением их по весам. Переноска, кантовка, подъем и навешивание полюсов производятся с помощью специальных приспособлений (рис. 9-13). Полюсы навешиваются группами по три-четыре полюса так, чтобы группы с одинаковыми весами располагались диаметрально одна против другой. При навешивании производится проверка высотной установки полюсов относительно средней линии ротора.
Для этого штифт проверочной стрелы устанавливается на роторе по риске средней линии ротора и затем поворотом стрелы проверяется ранее намеченная середина каждого полюса. Положение полюсов по высоте регулируется домкратами с, последующей постановкой подкладок на упоры или перемещением упоров.
По окончании высотной проверки полюсов устанавливаются и туго забиваются в пазы парные клинья до тех пор, пока не будет достигнута плотность установки хвостов полюсов в пазах. Расклинивание полюсов производится в нагретом состоянии. Окончательное расклинивание полюсов целесообразно выполнять одновременно с расклиниванием обода. Выступающие тонкие концы клиньев с нижней стороны затем обрезаются заподлицо, а с верхней стороны оставляется толстый конец клиньев каждого полюса высотой до 200 мм для возможности выема полюса. Обрезанные клинья обода и полюсов прихватываются электросваркой. Одновременно с расклиниванием производится окончательная проверка концентричности и высотной установки полюсов с помощью поверочной стрелы. Неконцентричность ротора определяется по полусумме зазоров между штифтом поверочной стрелы вверху и внизу каждого полюса. Проверяется также торцевой бой тормозного диска.
Пайка межполюсных соединений производится по окончании постановки и выверки полюсов. При этом соединительные пластины тщательно подгоняются одна к другой и рихтуются. Пайка соединительных пластин должна быть высококачественной и выполнена оловянистым припоем с бескислотным флюсом. Для большей надежности соединений применяется также серебряный припой. Местные разрывы соединительных пластин и пустоты в пайках не допускаются. Качество пайки межполюсных соединений можно проверить, пропуская через обмотки полюсов ток порядка 0,8 номинального и прощупывая нагрев в местах соединения пластин. После пайки межполюсных соединений устанавливаются соединительные планки демпферной обмотки, а также соединяются и паяются токоподводы.
При установке вентиляторных лопастей сверху и снизу обода ротора необходимо проверить их высотное положение и горизонтальность с помощью проверочной стрелы. Отклонения от горизонтальности не должны превышать ±5 мм.
Собранный ротор внимательно осматривается с тем, чтобы внутри и снаружи его не остались незакрепленные детали, а все гайки были зафиксированы электросваркой или специальными замками. После окончания сборки ротор очищается от пыли обдувкой сухим воздухом. Затем все детали ротора, за исключением вала и тормозных плит, окрашиваются лаком с помощью краскопульта.
Установка ротора на место.
Опускание ротора генератора в статор является наиболее ответственной монтажной операцией, так как вес ротора с устройством для его подъема на крупных генераторах достигает 900 т. Для успешного осуществления этой операции должен быть выполнен ряд соответствующих подготовительных работ. Ниже приводится последовательность установки в статор ротора подвесного генератора.
Подъем и транспортировка ротора крупного генератора, собранного на монтажной площадке с валом, производятся обычно двумя кранами с помощью специальной траверсы, подвешиваемой к их крюкам. Для захвата ротора в середине траверсы смонтировано устройство, состоящее из опорной втулки с двумя цапфами, опирающимися на подшипники, установленные на балках траверсы. На эту втулку опирается специальный подпятник, на котором расположено опорное разрезное кольцо, входящее в выточку вала генератора и являющееся захватом ротора.
Ротор, подвешенный на захватном устройстве, имеет возможность поворота на подпятнике и наклона вдоль траверсы. Такая подвеска ротора равномерно загружает оба крана и дает возможность исправления перекосов траверсы при подъеме и опускании ротора путем включения или выключения механизма подъема соответствующего крана. В связи с тем что при подъеме ротора оба крана работают с максимальной грузоподъемностью, перед транспортировкой каждого ротора следует тщательно проверить исправность и работу кранов и их механизмов. Кроме того, для проверки возможности транспортировки ротора над смонтированными агрегатами необходимо подвешенную к кранам траверсу без ротора поднять до крайнего верхнего положения крюков и определить зазор между нижней частью транспортируемого ротора и смонтированными агрегатами, который должен быть не менее 200 мм.
Рис: 9-14. Опускание ротора подвесного генератора в статор.
До установки ротора в кратере агрегата заканчивается подводка воздухопроводов к тормозам и проверяется действие их маслом от гидравлического пресса. На тормозные колодки, которые воспринимают вес ротора и должны быть в одной горизонтальной плоскости, ставятся фанерные подкладки толщиной 6—8 мм, выравнивающие негоризонтальность отдельных колодок тормозов, вследствие чего давление от ротора распределяется между колодками более равномерно.
Для предохранения обмотки статора от повреждения при проходе ротора через статор заготовляется 10—12 строганых мерных деревянных пластин толщиной в половину воздушного зазора и шириной 100-150 мм.
По окончании подготовительных работ начинается подъем ротора подтягиванием траверсы кверху до напряженного состояния тросов крана с одновременной проверкой горизонтальности траверсы. После этого фланец вала отсоединяется от монтажной плиты и ротор приподнимается над полом машинного здания. Крюки кранов необходимо устанавливать при этом строго вертикально над концами траверсы, так как иначе ротор, отсоединенный от монтажной плиты, качнется в начале подъема и может повредить фланец вала.
Для дополнительной проверки исправности кранов и особенно их тормозных устройств поднятый над монтажной площадкой ротор несколько раз немного приподнимается и резко останавливается. После этого ротор поднимается до крайнего верхнего положения крюков и переносится к агрегату.
Во время перемещения ротора над установленными агрегатами необходимо следить за тем, чтобы крылья нижнего вентилятора не задели за верх смонтированного агрегата. При подъеме, перемещении и опускании ротора нужно все время соблюдать горизонтальность траверсы, исправляя положение ее остановкой более опущенного крюка. Включение обоих кранов на подъем, перемещение и опускание должны быть строго одновременными.
Опущенный к статору ротор (рис. 9-14) останавливается для направления его более точно по расточке статора. С целью предотвращения повреждения обмотки статора при опускании ротора в воздушный зазор закладываются деревянные пластины, которые при этом беспрерывно опускаются и поднимаются.
Рис. 9-15. Приспособление для измерении воздушного зазора генератора. 1 — шкала отсчетов; 2 — рукоятка; 3 — подвижной клин; 4 — вилка; 5 — реечная вилка.
Отсутствие защемления пластины покажет, что ротор опускается нормально и обмотка статора не повреждается. В случае защемления пластины с какой-либо стороны опускание ротора прекращается и перемещением кранов пластина освобождается.
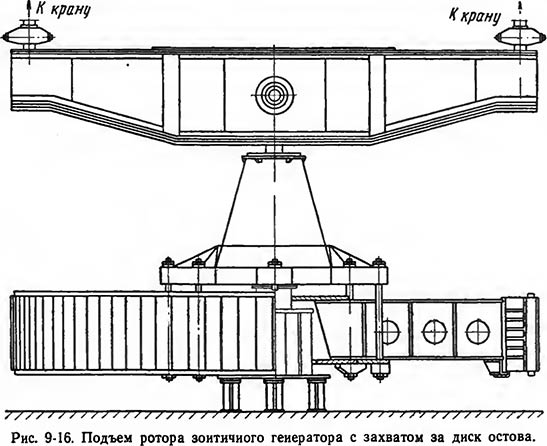
Перед установкой на место ротор поворачивается на траверсе так, чтобы монтажные метки на фланцах валов генератора и турбины совпали, а расхождение образующих фланцев было как можно меньше, после чего ротор опускается на колодки тормозов и, не отсоединенный от крана, предварительно прицентровывается к валу турбины.
Рис. 9-17. Транспортировка ротора зонтичного генератора.
Предварительная прицентровка ротора производится следующим образом. С помощью линейки, прикладываемой к образующим фланцев, замеряется величина несоосности ротора валу турбины и определяется ее направление. Замерами зазоров между фланцами определяются наклон вала генератора и величина необходимого подъема или опускания ротора на тормозах с соответствующей стороны. Затем ротор приподнимается кранами на 20—30 мм, фланец его вала отжимается в нужную сторону, изменяется толщина подкладок на тормозах и ротор снова опускается на место.
Предварительная прицентровка ротора должна производится до тех пор, пока несоосность валов достигнет величины не более 0,5—1,0 мм, а непараллельность плоскостей фланцев будет находиться в пределах 0,1— 0,2 мм.
Проверяется также предварительно воздушный зазор между ротором и статором по верху и по низу полюсов. Замеры зазоров удобно производить специальным щупом, показанным на рис. 9-15, представляющим собой раздвижной клин. При повороте маховичка рукоятки подвижной клин перемещается в зазоре до упора, а на шкале отсчета в это время показывается величина воздушного зазора. С помощью этого щупа можно замерять воздушные зазоры от 15 до 35 мм на глубине до 600 мм.
Подъем ротора зонтичного генератора, собранного на монтажной площадке без вала, осуществляется с помощью захватного устройства, соединенного шпильками с нижним диском остова и подвешенного к траверсе кранов (рис. 9-16). При подъеме и транспортировке такого ротора усилия от его веса должны распределяться равномерно по всей окружности нижнего диска, так как иначе вследствие недостаточной жесткости ротора могут произойти недопустимые перекосы его. Поэтому необходимо обращать особое внимание на то, чтобы затягивание всех шпилек, соединяющих захватное устройство с нижним диском, производилось равномерно. Транспортировка и опускание ротора аналогичны таким же операциям при установке ротора подвесного генератора. Транспортировка ротора крупного зонтичного генератора показана на рис. 9-17. Установка опущенного ротора производится на диск собранного подпятника без предварительной прицентровки. При посадке на втулку вала ротор направляется с помощью конусных шпилек, устанавливаемых в соответствии с маркировкой отверстий на втулке и в дисках.