2-4. НАПЛАВКА УПЛОТНИТЕЛЬНЫХ ПОВЕРХНОСТЕЙ АРМАТУРЫ
А. Характеристики электродов
Необходимость обеспечить надежную герметичность и стойкость затворов арматуры при длительной эксплуатации и стремление к максимальной экономии высоколегированных материалов привели к широкому распространению наплавки различных сплавов на детали затвора. Установлено, например, что наплавки по сравнению с применением уплотнительных колец, выполняемых путем механической обработки соответствующих заготовок, дают экономию до 70—80%.
Развитию методов наплавки способствовали систематические работы по изысканию и исследованию новых марок наплавляемых сплавов и, в особенности, совершенствование техники сварки — внедрение автоматического и полуавтоматического оборудования для наплавки уплотнительных поверхностей арматуры.
Материалы, применяемые в арматуростроении для наплавки уплотнительных поверхностей арматуры, могут быть разделены на следующие три основные группы: аустенитные нержавеющие стали, ферритные нержавеющие стали и твердые сплавы.
Аустенитные стали, предназначенные для наплавки, обладают довольно высоким сопротивлением к коррозионному и эрозионному воздействиям рабочей среды. Наплавка выполняется без предварительного подогрева деталей и, как правило, без последующей термической обработки. Однако эти стали обычно имеют невысокую поверхностную твердость (не выше 220 единиц по Бривелю), которая не может обеспечить надлежащего качества уплотнительных поверхностей в запорной арматуре высокого давления, а также в арматуре, предназначенной для рабочих сред, содержащих твердые частицы. Эта группа сталей имеет повышенную склонность к задиранию. При наплавке аустенитных сталей на ферритную основу приходится иногда считаться также с большой разницей коэффициентов теплового расширения. Все это значительно ограничивает применение аустенитных сталей как наплавочного материала для арматуры. Их применение можно считать приемлемым для некоторых типов регулирующих клапанов, работающих в условиях интенсивности эрозионного износа и в тех случаях, когда к этим клапанам не предъявляются высокие требования в отношении герметичности затвора.
В вентилях с плоскими уплотнительными поверхностями, где клапан (тарелка) перемещается вдоль осн, перпендикулярной седлу, и в момент закрытия вентиля только прижимается своей уплотнительной поверхностью к поверхности седла, опасность задирания отсутствует.
На Венюковском арматурном заводе аустенитные электроды марки ЦТ-1 применяются для наплавки уплотнительных поверхностей вентилей, работающих при температуре не выше 510° С. Для более высокой температуры применяются в основном электроды марки ЦН-6.
На ремонтных заводах энергосистем наплавку уплотнительных поверхностей вентилей и задвижек, работающих при температуре не выше 510° С, производят аустенитными электродами марки ЦЛ-ЗМ. Из-за склонности к задиранию уплотнительных поверхностей, наплавляемых электродами марки ЦЛ-ЗМ, в настоящее время ведутся работы по замене этих марок электродов другими, более твердыми сплавами.
На Барнаульском котельном заводе до 1959 г. уплотнительные поверхности на задвижках наплавляли электродами марки ЦТ-1, но вследствие задирания наплавленного металла при температуре 450°С завод перешел на наплавку хромистыми электродами типа 2X13. Уплотнительные поверхности на вентилях Dу20 и более наплавляют непосредственно на корпус электродами марки ЦТ-1.
В ФРГ для наплавки уплотнительных поверхностей кованой и штампованной арматуры применяют некоторые марки аустенитных сталей, имеющих повышенную твердость, например терманит D (0,1—0,2% С, 1,8— 2,3% Si, 0,2—0,4% Мп, 19—20% Ст и 10%Ni; твердость 40 Rc) и терманит X (<0,22% С, 0,5—1% Si, 5,5— 6,5% Мп, 17—19% Ст и 7,5—8,5% Ni; твердость 42 Rс).
В американском арматуростроении в последние годы наплавка уплотнительных поверхностей аустенитными сталями почти не применяется.
Ферритные (хромистые) нержавеющие стали имеют более высокую твердость и стойкость в отношении задирания, чем аустенитные хромоникелевые стали, но отличаются низкой эрозионной устойчивостью. Их применение можно считать приемлемым для запорной паровой арматуры в тех случаях, когда не предъявляются высокие требования в отношении эрозионного износа. На Барнаульском котельном заводе хромистые электроды марки 2X13 применяются для наплавки уплотнительных поверхностей (тарелки, кольца) задвижек. Такие же марки электродов применяются на заводах, поставляющих арматуру для судостроения.
Западногерманская фирма «Штальарматурен-Белекке», согласно каталожным данным 1954 г., применяет для уплотнительных поверхностей дисков и клиньев задвижек ферритную хромистую сталь марки терманит 17 Сг (<0,1% С, 0,3—0,5% Si, 0,2—0,4% Мп и 17— 18% Сг; твердость 40—45 Rc).
Проведенные испытания показали, что хромистые стали по сравнению со стеллитами имеют более низкую устойчивость против задирания.
Стеллиты — твердые сплавы на кобальтовой основе, обладающие высокой стойкостью против эрозии и задирания. Из выпускаемых в настоящее время отечественной промышленностью и за рубежом аналогичных сплавов они являются наилучшими. Опыт эксплуатации ряда электростанций показывает, что уплотнительные поверхности арматуры, наплавленные стеллитом, работают надежно в течение 10—12 лет.
На Венюковском арматурном заводе стеллиты ЦН-2 и ВЗК применяют для наплавки уплотнительных поверхностей арматуры, работающей при температуое до 600° С.
В ФРГ за последние годы также все более расширяется применение наплавки уплотнительных поверхностей кобальтовыми стеллитами. Таковыми являются тицит, акрит и перцит (1,2% С, 27% Сг, 65% Со), цельзит (1,2% С, 28% Сг и 65% Со), ракса (1,3% С, 28% Сг и 65% Со).
Арматурная промышленность США имеет почти двадцатилетний опыт применения изделий с наплавками из кобальтовых стеллитов. Преимущественное распространение здесь получил стеллит № 6, по своему химическому составу соответствующий нашему сплаву марки ВЗК. В США наряду со стеллитами применяются следующие твердые сплавы на никелевой основе: сплав № 1 (76% Ni, 13% Сг и 3% В); сплав № 2 (70% Ni, 17% Сг и 4% В); хестелой С (57% Ni, 15% Сг; 17% Мо и 5% W), колманой С (68% Ni, 18% Сг и 4% В). Эти сплавы получили особенно широкое распространение в тех случаях, когда наряду с сохранением твердости, стойкости против задирания и эрозии предъявляется требование корозионной устойчивости в различных агрессивных средах.
Большой опыт по наплавке твердыми сплавами уплотнительных поверхностей арматуры ацетилено-кислородным пламенем имеется на чехословацких арматурных заводах. В табл. 2-3 приведены марки и химический состав в процентах наплавочных материалов, применяемых в Чехословакии.
Наибольшее распространение получили стеллитовые сплавы Real 095 и Real 096. Твердость первого сплава составляет 430—490 Hv, а другого (с меньшим содержанием углерода и вольфрама)—370—420 Ην. Как заменяющий материал для менее ответственной арматуры применяется сплав ZAZlOCo, твердость которого около 400 Hv. Для работы при сверхкритических параметрах пара в Чехословакии применяются твердые сплавы, приведенные в табл. 2-4.
Б. Технология наплавки
Наплавка хромоникелевыми электродами ЦТ-1 типа ЭА-4 по ГОСТ 2523-51 (стержень Св из 0Х18Н9) и ЦЛ-ЗМ тип ЭА-1 по ГОСТ 2523-51 (стержень Св из 1Х18Н9Т).
Разделка канавок для наплавки уплотнительных поверхностей должна производиться без прямых или острых углов. Наплавку уплотнительных поверхностей на литых корпусах арматуры нужно делать после гидравлического испытания их на прочность.
Таблица 2-3
Таблица 2-4
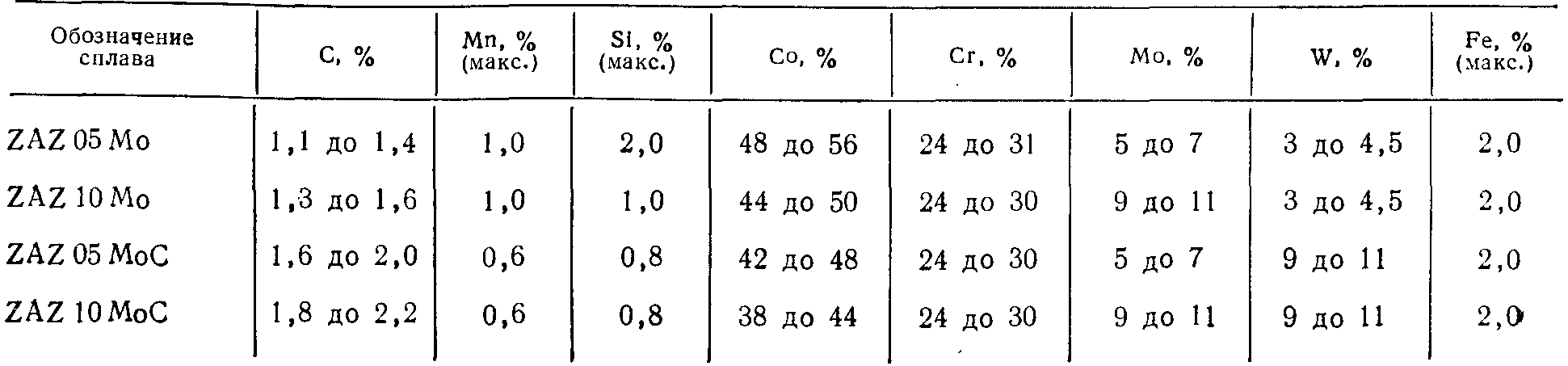
Наплавка производится постоянным током при обратной полярности (плюс на электроде). Сила сварочного тока зависит от диаметра электрода и принимается: для электродов d=4 мм ί=130—150 а и для d = 5 мм i— = 150—180 а. Перед наплавкой деталь следует устанавливать так, чтобы наплавляемый участок находился в горизонтальном положении. Количество расплавленного основного металла должно быть как можно меньше. Наплавку производить в три слоя. После наплавки каждого слоя следует тщательно очистить поверхность наплавки от брызг и шлака. Электрод в процессе наплавки должен держаться под углом 10—15° к вертикали в сторону его перемещения. Скорость его перемещения зависит от скорости расплавления. Общая высота наплавленного слоя должна составлять 6—9 мм. Наплавку следует производить при возможно короткой дуге и беспрерывным швом в одном направлении; начало шва должно перекрываться на 10—15 мм.
Контроль качества наплавки производится наружным осмотром и проверкой размеров наплавленного металла. Толщина и ширина наплавленного слоя должны иметь припуск на механическую обработку 1,5—2 мм. На наплавленной поверхности после механической обработки не должно быть раковин, пузырей, шлаковых включений, выкрашивания и трещин.
Наплавка хромистыми электродами 1X13
Поверхность под наплавку после механической обработки не должна иметь прямых или острых углов, глубоких рисок и заусенцев. Не должно быть также пороков в виде земляных, шкаловых или газовых раковин, трещин и рыхлот.
Перед наплавкой детали нагревают до температуры 300—400° С. Наплавку осуществляют постоянным током при обратной полярности (плюс на электроде). Сила сварочного тока для электродов d = 4 мм составляет 140—160 а и для электродов d = 5 мм 180—200 а. Наплавка производится в четыре слоя одинаковой толщины (1,5—2 мм).
После наплавки детали подвергают отпуску в нагревательных печах. Температура нагрева для всех типов деталей должна быть в пределах 580 ±5° С, и выдержка при этой температуре 3,5 ч. Охлаждение деталей после отпуска производится вместе с печью до температуры 200° С, после чего детали остывают на открытом воздухе.
Для проверки твердости и химического состава наплавки изготовляют контрольный образец. Наплавка и термическая обработка образца производятся по тем же режимам, как и самих деталей. Твердость по Бринелю должна находиться в пределах 350—470.
Наплавка нержавеющими электродами ТК.З-А и ТК.З-АТ (стержень Св Х25Н13 по ГОСТ 2246-51)
Канавки под наплавку должны иметь плавные переходы внутри выточек. Острые и прямые углы в разделке, которые могут стать местом зашлакования, не допускаются. Поверхность, подлежащую наплавке, зачищают от грязи, масла и ржавчины до металлического блеска.
Детали (тарелки, стаканы), требующие пониженной твердости наплавок (порядка Hв=150—180), наплавляют электродами с покрытием ТКЗ-АТ, а детали, требующие повышенной твердости (порядка Hв = 220—270), наплавляют электродами ТКЗ-А. Наплавочные работы производятся на постоянном токе при обратной полярности (плюс на электроде).
Режимы сварки обоих электродов следующие:
Диаметр электрода, мм | Сила тока, а |
3 | 100—130 |
4 | 130—150 |
5 | 150—180 |
Наплавляемая поверхность при сварке должна находиться в нижнем положении. Наплавку следует делать в три слоя, толщиной 2—3 мм каждый, при диаметре электрода 3 мм и толщиной 3—4 мм при диаметре электрода 5 мм.
После наплавки каждого слоя валик охлаждают до температуры 50—60° С на открытом воздухе. Каждый предыдущий слой перед наложением последующего тщательно зачищают от шлака и брызг. Начало каждого слоя следует очистить от шлака и перекрыть на 10— 15 лиг.
При смене электрода или при обрыве дуги кратер должен быть заделан пульсирующей дугой, тщательно очищен и проверен на отсутствие трещин. Обнаруженные трещины удаляют проточкой дефектного слоя до чистого металла и только после этого продолжают наплавку. Удаление трещин проверяют путем осмотра. Сомнительные места подвергают травлению.
Наплавленный металл должен быть чистым, плотным, без шлаковых включений и трещин.
Наплавка электродом марки ЦН-6 деталей, работающих до температуры 600°С (стержень Св 0Х18Н9 по ГОСТ 2246-54)
Покрытие электрода состоит из 30% мрамора, 59% окиси титана, 27% ферросилиция и 25—30% жидкого стекла. Химический состав наплавленного металла должен быть: 3=0,15 С, 5—5,8% Si, 1—2% Мп, 16—18% Сг, 6—8% Ni, 0,04% S и 0,04% Р. Твердость после наплавки должна быть в пределах 28—32 Rc. Электрод ЦН-6 в настоящее время является основным наплавочным материалом для арматуры высоких параметров, применяемым ВАЗ и электростанциями.
Согласно данным отдела сварки ЦНИИТМАШ электрод ЦН-6 прошел ряд испытаний и показал хорошие результаты. Образцы, наплавленные этим электродом, подвергались нагреву до температуры 650° С, выдержке при этой температуре 15 мин и охлаждению на открытом воздухе. Было проведено 50 испытаний на воздействие теплосмен, причем не обнаружено трещин на наплавленной поверхности ни до, ни после механической обработки.
Во ВТИ было проведено испытание сплава К-4 (ЦН-6) на эрозию в условиях воздействия горячей воды при температуре 210°С и давлении 220 кг/см\ протекающей со скоростью и = 140 м/сек. В качестве эталона параллельно испытывался в таких же условиях образец из стойкой против эрозии стали 1Х18Н9Т. В результате этих испытаний был сделан вывод, что эрозионная стойкость сплава К-4 удовлетворяет требованиям, предъявляемым к материалам уплотнительных поверхностей арматуры высокого и сверхвысокого давлений.
Для наплавки применяют электроды диаметром 4— 5 мм. Перед наплавкой поверхности детали в этом месте и на прилегающих участках очищаются от загрязнений.
На деталях, основной металл которых не требуют подогрева (сталь 20 или 1Х18Н9Т), наплавку можно производить без предварительного подогрева. Остальные детали подогревают до температуры, соответствующей температуре подогрева основного металла, например, сталь 38ХВФЮ до температуры 400—450° С; сталь 20ХМФЛ—до 300—350° С; сталь 12ХМФ —до 300— 350° С; сталь 15Х1М1ФЛ — до 300—350° С и сталь 20ХМЛ — до 200—250° С. После наплавки детали охлаждают в песке до комнатной температуры.
Наплавка производится на постоянном токе при обратной полярности и в нижнем положении. Сила тока для электрода d=4 мм принимается равной 120—140 а и для электрода d=5 мм 180—200 а. Во время наложения первого слоя расплавление основного металла должно быть минимальным, для чего наплавку необходимо вести при минимальной силе тока.
Детали больших габаритов (Ду 175 и более) следует наплавлять обратно ступенчатым методом, для чего окружность наплавки разбивается на четыре части. Кратер должен быть полностью заплавлен и выведен за габариты наплавки. Участки верхнего слоя начинают наплавлять с середины участков нижнего слоя и наплавку ведут в противоположном направлении. Наплавленные детали должны иметь припуск на механическую обработку по ширине 2,5—3 мм на сторону и по высоте 2—3 мм.
Наплавку рекомендуется выполнять короткой дугой с поперечным колебательным движением электрода на всю ширину наплавляемой поверхности, не допуская короткого замыкания.
Детали небольших габаритов (до £)у 40) можно наплавлять ванным методом. После наплавки каждого валика необходимо производить тщательное удаление шлака. Для устранения внутренних (сварочных) напряжений все наплавленные тарелки задвижек и клапанов подвергают термической обработке по режиму: нагрев до температуры 700° С, выдержка при этой температуре 8 ч и последующее медленное охлаждение в нагретом песке или вместе с печью. Наплавленные детали подвергают наружному осмотру до и после механической обработки.
На наплавленной поверхности не должно быть дефектов в виде опор, трещин или шлаковых включений. Обнаруженные дефекты в наплавленной поверхности на любой стадии изготовления арматуры могут быть исправлены по режиму, указанному выше.
Наплавка электродом марки ЦН-8 (стержень Св из Х25Н13) деталей арматуры, работающих при температуре 650° С
В условиях воздействия пара при температуре 650°С и давлении 800 кг/см2 наплавленный электродами марки ЦН-8 металл обладает стойкостью против эрозии и задираемости, а также противостоит межкристаллитной и общей коррозии.
Химический состав наплавленного металла: 0,08— 0,12% С, 8—9% Si, 19—22% Сг, 10—12% Ni, 0,04% S и 0,4% Р. Микроструктура наплавки — легированный феррит. Твердость после наплавки составляет 45—55 Re.
Покрытие электродов применяется следующего состава: 21% мрамора (ГОСТ 4416-48), 27% плавикового шпага (ГОСТ 4421-48), 5% двуокиси и титана-5, 45— 47% ферросилиция (ГОСТ 4415-49), 25—30% раствора селиката натрия по отношению к сумме остальных компонентов (ГОСТ 4419-48).
Отношение веса покрытия и непокрытой части стержня электрода составляет 69—73%· Ориентировочная толщина покрытия (на сторону) для электродов d = 4 мм должна составлять 1 мм и для электродов d=5 мм 1,3 мм.
Хранение электродов, упакованных в соответствии с ГОСТ 9466-60, производится в закрытом помещении. Через каждый год хранения электроды подвергают прокалке и повторному испытанию.
Наплавка производится на постоянном токе при обратной полярности. Средние рекомендуемые режимы тока для электродов диаметром 4 мм 120—140 а и диаметром 5 мм 180—200 а.
Заготовки, подготовленные к наплавке, нагревают до температуры 700° С. В процессе наплавки температура заготовки не должна быть ниже 600° С. Наплавленные детали охлаждают в горячём песке или вместе с печью.