Обобщение данных, проведенное ОАО «Фирма ОРГРЭС» на 01.01.2000 (табл. 1.11), показало, что на большинстве энергоблоков паропроводы отработали парковый ресурс или имеют длительную наработку, приближающуюся к срокам паркового ресурса.
Таблица 1.11. Длительность наработки паропроводов энергетических блоков мощностью 150-1200 МВт
Мощность энергоблока, параметры пара | Типоразмер паропроводов Dн х s, мм | Марка | Парковый ресурс паропроводов, ТЫС. ч | Количество энергоблоков с наработкой паропроводов на 01.01.2000, тыс. ч | ||
До 150 | 151-250 | Более 250 | ||||
150-200 МВт, | 273 х 36 | 12Х1МФ | 250 | — | 15 | 15 |
273 х 32 | 12Х1МФ | 220 | — | 5 | 1 | |
219 х 28 | 12Х1МФ | 250 | — |
| 1 | |
219 х 30 | 15Х1М1Ф | 250 | — | — | 3 | |
325 х 43 | 12Х1МФ | 250 | — | 15 | 4 | |
325 х 38 | 12Х1МФ | 210 | 49 | 27 | — | |
150-200 МВт, | 426 х 18 | 12Х1МФ | 250 | 21 | 32 | 8 |
426 х 19 | Ϊ2Χ1ΜΦ | 250 | 5 | — | 2 | |
426 х 20 | 15ХМ | 250 | — | — | 1 | |
426 х 17 | 12Х1МФ | 250 | — | 16 | 2 | |
426 х 16 | 12Х1МФ | 250 | — | 2 |
| |
465 х 19 | 12Х1МФ | 250 | — | 4 | 1 | |
465 х 20 | 12Х1МФ | 250 | — | 5 | 8 | |
465 х 22 | 12Х1МФ | 250 | — | 1 | 2 | |
630 х 25 | 15Х1М1Ф | 270 | 10 | — | — | |
630 х 28 | 15Х1М1Ф | 270 | 9 | — | — | |
250-300 МВт, | 245 х 45 | 15Х1М1Ф | 250 | — | 52 |
|
245 х 48 | 15Х1М1Ф | 250 | 1 | — | — | |
325 х 56 | 15Х1М1Ф | 250 | — | 4 | — | |
325 х 60 | 15Х1М1Ф | 250 | 24 | 18 | — | |
273 х 62,5 | 12Х1МФ | 250 | — | 7 | — | |
219 х 32 | ЭИ-756 | 250 | — | 1 | — | |
250-300 МВт, | 426 х 16 | 12Х1МФ | 250 | — | 21 | — |
426 х 17 | 12Х1МФ | 250 | — | 4 | — | |
426 х 18 | 12Х1МФ | 250 | — | 25 | — | |
426 х 19 | 12Х1МФ | 250 | 1 | 4 | — | |
426 х 20 | 12Х1МФ | 250 | — | 1 | — | |
630 х 25 | 15Х1М1Ф | 270 | 19 | 22 |
| |
630 х 28 | 15Х1М1Ф | 270 | 5 | — | — | |
465 х 20 | 15Х1М1Ф | 250 | 2 | — | — | |
485 х 20 | 15Х1М1Ф | 250 | 2 | — |
| |
500 МВт, | 273 х 45 | 15Х1М1Ф | 100 | 6 | — | — |
377 х 60 | 15Х1М1Ф | 100 | 6 |
|
| |
500 МВт, | 550 х 25 | 15Х1М1Ф | 150 | 6 | — | — |
720 х 22 | 15Х1М1Ф | 150 | 6 | — | — |
Окончание табл. 1.11
Мощность энергоблока, параметры пара | Типоразмер паропроводов DH X s, мм | Марка | Парковый ресурс паропроводов, тыс. ч | Количество энергоблоков с наработкой паропроводов на 01.01.2000, тыс. ч | ||
До 150 | 151-250 | Более 250 | ||||
800 МВт, | 465 х 75 | 15Х1М1Ф | 110 | 14 |
|
|
800 МВт, | 630 х 25 | 15Х1М1Ф | 270 | 5 | — | — |
630 х 28 | 15Х1М1Ф | 270 | 7 | — | — | |
920 х 32 | 15Х1М1Ф | 100 | 12 |
|
| |
465 х 19 | 12Х1МФ | 130 | 2 | — | — | |
1200 МВт, | 377 х 60 | 15Х1М1Ф | 100 | 1 |
|
|
1200 МВт, 4 МПа, 545 °C (промперегрев) | 720 х 25 | 15Х1М1Ф | 150 | 1 |
|
|
К этому следует добавить, что отдельные энергоустановки с давлением пара перед турбиной 9 МПа имеют наработку более 350 тыс. ч, а с давлением 13 МПа — около 300 тыс. ч. Пять энергоблоков имеют наработку более 270 тыс. ч. На многих энергоустановках паропроводы работают без замены с начала эксплуатации.
Из результатов статистического анализа повреждений паропроводов ТЭС в период 1996-1999 гг. [84] установлено следующее.
Повреждаемость паропроводов блочных энергоустановок характеризуется числом отказов 0,244 отк./1 млн кВт и установок с поперечными связями — 0,649 отк./1 млн кВт, соответственно, где 1 отк./1 млн кВт — 1 отказ на 1 млн кВт установленной мощности.
В первую очередь это можно объяснить возрастной характеристикой оборудования. Энергоустановки ТЭС с поперечными связями отличаются большей наработкой оборудования.
Так, на конец 1996 г. наработку более 100 тыс. ч имели 70,4% энергоблоков по количеству и 63,5% по установленной мощности; для турбин ТЭС с поперечными связями (давлением 13 и 9 МПа) — 85,4 и 76,2%, соответственно. Дополнительным фактором повышенной повреждаемости отдельных паропроводов ТЭС с поперечными связями служат трубы с толщиной стенки, не обеспечивающей нормативного запаса прочности (например, трубы 0273 X 17 мм из стали 12Х1МФ на параметры 540 °C и 10 МПа).
Повреждения паропроводов, вызвавших отказы блочных энергоустановок, распределены следующим образом:
паропроводы свежего пара—28%;
паропроводы горячего промперегрева—58%;
паропроводы холодного промперегрева—14%.
Четверть всех повреждений паропроводов отечественных ТЭС относятся к опасным — разрывы элементов (гибов, сварных соединений и редко — прямых труб); 82,5% общего количества повреждений приходится на сварные соединения, а 17,5% относится к гибам.
Повреждения паропроводов в целом вызваны следующими причинами: повышенные (непроектные) напряжения—24%;
дефекты сварки—22%;
металлургические дефекты и непроектные материалы —19%;
исчерпание ресурса металла—19%;
коррозия—16%.
В том числе повреждения гибов паропроводов: исчерпание ресурса металла—39%;
коррозия—33%;
металлургические дефекты—28%.
Повреждения сварных соединений паропроводов обусловлены: дефектами сварки—46%;
исчерпанием ресурса—33%;
повышенными (непроектными) напряжениями—21%.
Эксплуатационные повреждения элементов паропроводов по отчетности ТЭС за период 1996-1999 гг. характеризуются относительно небольшим числом отказов (табл. 1.12). Статистические данные о поврежденности элементов паропроводов по месту и причинам отказов приведены в табл. 1.13.
Из анализа отказов следует, что наибольшая повреждаемость отмечается на паропроводах ТЭС с поперечными связями — 32 случая из 44, или 73%. При этом установленная мощность ТЭС с поперечными связями составляет 93% мощности блочных тепловых электростанций. Блочные ТЭС отличаются несколько большей повреждаемостью паропроводов горячего промперегрева по сравнению с паропроводами свежего пара (58% против 42%).
Наиболее повреждаемыми элементами паропроводов являются сварные угловые швы в местах приварки штуцеров (45% общего количества повреждений), затем стыковые сварные соединения (36%) и гибы (14%).
Таблица 1.12. Повреждения элементов главных паропроводов ТЭС с параметрами пара 10 МПа и выше за 1996-1999 гг.
Год | Типоразмер паропроводов, DH х s, мм | Марка стали | Расчетные параметры пара | Наработка, | Место | Причина повреждения | |
р, МПа | t, °C | ||||||
1996 | 426 х 18 | 12Х1МФ | 2,4 | 545 | 125 | Узел приварки штуцера к паропроводу | Повышенные напряжения |
325 х 28 | 12Х1МФ | 13,0 | 550 | 265 | Сварной шов | Исчерпание ресурса | |
273 х 32 | 12X1 МФ | 14,0 | 560 | 196 | Гиб | То же | |
273 х 60 | 12Х1МФ | 25,5 | 545 | 153 | То же |
| |
426 х 18 | 12Х1МФ | 2,4 | 545 | 236 | Сварной шов | » | |
426 х 18 | 12Х1МФ | 3,7 | 545 | 185 | То же | » | |
426 х 18 | 12Х1МФ | 3,7 | 545 | 153 | » | Не установлено | |
273 х 22 | 12МХ | 9,0 | 500 | 336 |
| Загрязненность металла шлаковыми включениями | |
273 х 15 | 12Х1МФ | 10,0 | 510 | 300 | Узел приварки байпаса к паропроводу | Исчерпание ресурса | |
273 х 36 | 12Х1МФ | 14,0 | 560 | 73 | Узел приварки дренажа к паропроводу | Дефект монтажной сварки | |
219 х 25 | 12Х1МФ | 13,0 | 550 | 114 | Узел приварки байпаса к паропроводу | То же | |
1997 | 273 х 36 | 12Х1МФ | 14,0 | 560 | 214 | Узел приварки дренажа к паропроводу | » |
325 х 38 | 12Х1МФ | 14,0 | 545 | 174 | Узел приварки штуцера к паропроводу | » | |
273 х 32 | 12Х1МФ | 13,0 | 550 | 194 | Прямой уча | Исчерпание ресурса | |
377 х 45 | 15Х1М1Ф | 13,0 | 550 | 112 | Узел приварки дренажа к паропроводу | Дефект монтажной сварки | |
273 х 20 | 12Х1МФ | 10,0 | 540 | 201 | То же | То же | |
273 х 32 | 12Х1МФ | 13,0 | 550 | 338 | Сварной шов | Исчерпание ресурса |
Продолжение табл. 1.12
Год | Типоразмер паропроводов, DH х s, мм | Марка стали | Расчетные параметры пара | Наработка, тыс. ч | Место повреждения | Причина повреждения | |
р, МПа | t, °C | ||||||
1998 | 465 х 75 | 15Х1М1Ф | 25,5 | 545 | 93 | Сварной шов | Дефект монтажной сварки |
325 х 65 | 15Х1М1Ф | 25,5 | 545 | 157 | То же | Повышенные напряжения из- за неполадок в опорно-подвесной системе | |
720 х 22 | 15Х1М1Ф | 4,0 | 545 | 130 | » | Не установлена | |
720 х 22 | 15Х1М1Ф | 4,0 | 545 | 119 | » | Повышенные напряжения от самокомпенсации | |
245 х 40 | Ϊ2Χ1ΜΦ | 13,0 | 550 | 104 | Узел приварки байпаса к паропроводу | Повышенные напряжения | |
273 х 32 | 12Х1МФ | 14,0 | 560 | 111 | Гиб | Исчерпание ресурса | |
325 х 38 | 15Х1М1Ф | 13,0 | 550 | 238 | Узел приварки байпаса к паропроводу | Дефект монтажной сварки | |
273 х 20 | 12Х1МФ | 10,0 | 540 | 216 | Сварной шов | Неполадки в | |
273 х 15 | 12Х1МФ | 10,0 | 510 | 25 | Прямой уча | Дефект ремонта; несоответствие марки | |
273 х 20 | 12X1 МФ | 10,0 | 540 | 27 | Узел приварки байпаса к паропроводу | Термическая усталость из-за недостатков эксплуатации | |
273 х 15 | 12Х1МФ | 10,0 | 510 | 288 | Узел приварки штуцера к паропроводу | Дефект мон | |
377 х 50 | 15Х1М1Ф | 13,0 | 550 | 13 | Узел приварки дренажа к паропроводу | Дефект монтажа |
Окончание табл. 1.12
Год | Типоразмер паропроводов, Dн х s, мм | Марка | Расчетные параметры пара | Наработка, | Место | Причина повреждения | |
р, МПа | 1, °C | ||||||
| 273 х 20 | 12Х1МФ | 10,0 | 540 | 210 | Сварной шов | Дефект изготовления |
273 х 32 | 12Х1МФ | 14,0 | 560 | 15 | Узел приварки байпаса к паропроводу | Дефект монтажной сварки | |
1999 | ’720 х 22 | 15Х1М1Ф | 4,0 | 545 | 125 | Сварной шов | Не установлена |
325 х 43 | 12Х1МФ | 14,0 | 545 | 240 | То же | Дефект монтажной сварки | |
219 х 25 | 12Х1МФ | 13,0 | 550 | 161 | Гиб | Исчерпание ресурса | |
219 х 25 | 12Х1МФ | 13,0 | 550 | 69 | То же | Дефект изгото | |
273 х 32 | 12Х1МФ | 14,0 | 560 | 99 | » | Исчерпание ресурса | |
325 х 38 | 12Х1МФ | 13,0 | 550 | 120 | Сварной шов | Дефект монтажной сварки | |
273 х 15 | 12Х1МФ | 10,0 | 510 | 322 | То же | Дефект монтажа | |
273 х 15 | 12Х1МФ | 10,0 | 510 | 35 | Узел приварки байпаса к паропроводу | Дефект ремонтной сварки | |
273 х 36 | 12Х1МФ | 13,0 | 550 | 186 | То же | Исчерпание ресурса | |
273 х 20 | 12Х1МФ | 10,0 | 540 | 122 | Узел приварки дренажа к паропроводу | Дефект ремонтной сварки | |
325 х 43 | 12Х1МФ | 13,0 | 550 | 304 | То же | Повышенные напряжения | |
273 х 36 | 12Х1МФ | 13,0 | 550 | 236 | » | То же | |
273 х 20 | 12Х1МФ | 10,0 | 540 | 115 | Узел приварки штуцера к паропроводу | Дефект монтажной сварки |
Таблица 1.13. Повреждаемость элементов паропроводов (табл. 1.12)
Год, количество отказов | Количество повреждений паропроводов | Место повреждения | Причина повр| | ||||||||
свежего пара | горячего промперегрева | Пря | Гибы | Стыковые сварные соединения | Сварные швы приварки штуцеров и дренажей | Нерасчетные напряжения | Дефекты | И | |||
заводского изготовления | монтажа | ремонта | Been | ||||||||
1996, | 7 | 4 | _ | 2 | 5 | 4 | 1 | _ | 1 | _ | 8 |
1997, | 6 | __ | 1 | _ | 1 | 4 | __ | __ | _ | _ | 6 |
1998, | 12 | 2 | 1 | 1 | 6 | 6 | 4 | _ | 2 | 2 | 4 |
1999, | 12 | 1 | _ | 3 | 4 | 6 | 2 | 1 | __ | 1 | 8 |
Всего | 37 | 7 | 2 | 6 | 16 | 20 | 7 | 1 | 3 | 3 | 26 |
100 % | 84 | 16 | 5 | 14 | 36 | 45 | 16 | 2 | 7 | 7 | 59 |
Таблица 1.14. Статистические данные о повреждениях гибов труб общестанционной системы паропроводов, эксплуатирующихся в условиях ползучести
Группы гибов | Система | Гибы, шт. | В том числе | ||||
из стали | из стали | с наработкой в % от паркового ресурса | |||||
> 100 | 70-100 | <70 | |||||
1 | В системе паропроводов ТЭС | 24636 | 18105 | 6531 | 10547 | 8002 | 6087 |
2 | Дефектных или подвергнутых замене | 3977 | 2825 | 452 | 942 | 664 | 1671 |
2.1 | В том числе с макротрещинами | 138 | 122 | 16 | 85 | 12 | — |
2.2 | В том числе со сквозными трещинами, развившимися с наружной поверхности | 16 | 16 | 0 | 9 | 0 |
|
3 | Подвергнутых контролю микроповрежденности | 1684 | 1630 | 54 | 740 | 749 | 199 |
3.1 | В том числе содержащие микротрещины | 23 | 12 | 7 | 12 | 2 | — |
3.2 | В том числе содержащие микродефекты в виде цепочек микропор или множественных пор размером более 1 мкм | 461 | 444 | 21 | 286 | 125 |
|
4 | С относительной остаточной деформацией | 40 | 32 | 8 | 16 | 8 |
|
5 | С относительной овальностью менее 1% | 85 | 64 | 11 | 37 | 0 |
|
Наряду со статистическими данными фирмы АО «ОРГРЭС» по отказам элементов паропроводов были обобщены и проанализированы данные, полученные от более 80-ти ТЭС в ответ на запросы по типовым формам ОС «Живучесть ТЭС» (письма РАО «ЕЭС России» АК 17/230 от 02.09.99 и АК 17/7 от 11.01.2000).
Анализу был подвергнут массив данных по более чем 24 тыс. паропроводных гибов, эксплуатирующихся в условиях ползучести. Результаты обработки статистических данных приведены в табл. 1.14 и на рис. 1.25 и 1.26.
Рис. 1.25. Относительное количество гибов паропроводов из сталей 12Х1МФ и 15Х1М1Ф, находящихся в эксплуатации: (а) суммарное количество; (б) в зависимости от наработки тн; парковый ресурс (тп)
Рис. 1.26. Относительное количество дефектных или подвергнутых замене гибов: (а) доли от общего количества; (б) доли от общего количества дефектных и подвергнутых замене гибов в зависимости от наработки тн
В рассмотренных системах паропроводов ТЭС относительное количество гибов из стали 12Х1МФ составляет 73%, из стали 15Х1М1Ф — 27% (рис. 1.25,а).
Около 25% всех гибов имеют наработку менее 0,7 паркового ресурса (тп), 32% — наработку (0,7 ~ 1,0)тп и 43% — более 1,0тп (рис. 1.25,6).
Из общего числа гибов (24636) имели дефекты или были заменены 3277, или 13,3%. По данному показателю большую повреждаемость имеют гибы из стали 12Х1МФ (15,6%) по сравнению с гибами из стали 15Х1М1Ф (6,9%) — рис. 1.26,а. Интересно отметить, что 51% поврежденных гибов имел наработку менее 0,7тп, 20% — (0,7 4- 1,0)тп и 29% — более 1,0тп (рис. 1.26,б).
Контроль микроповрежденности проводился на 6,8% гибов, причем такому контролю подвергали 9% гибов из стали 12X1 МФ и менее 1% гибов из стали 15Х1М1Ф (рис. 1.27,а).
Из общего числа гибов, выполненных из стали 12Х1МФ, на которых проводилась оценка микроповрежденности (1630) на 12 (0,7%) обнаружены микротрещины и на 444 (27%) выявлены дефекты в виде цепочек пор или множественных пор размером более 1 мкм (рис. 1.27,б,в).
Из общего числа гибов из стали 15Х1М1Ф, подвергнутых контролю микроповрежденности (54), 7 гибов (13%) имели в металле микротрещины и 21 (38,8%) — цепочки пор или множественные микропоры (рис. 1.27,б,в).
Интересен тот факт, что из общего числа дефектных или замененных гибов (3277) только 40 (менее 1,2%) имели остаточную деформацию прямых участков более предельно допускаемой (0,8%) и 85 (2,6%) — относительную овальность менее 1% (табл. 1.12). Оба показателя считаются характерными для ускоренной ползучести гибов.
При статистическом анализе были использованы данные о характере повреждений замененных гибов из стали 12Х1МФ (табл. 1.15).
Рис. 1.27. Относительное количество гибов паропроводов, имеющих микроповрежденность металла, из сталей 12Х1МФ (1) и 15Х1М1Ф (2): (а) доля от количества проконтролированных; (б) содержащие микротрещины; (в) содержащие микродефекты в виде цепочек микропор или множественных пор
Комментируя данные табл. 1.15, можно отметить, что число трещин в нейтральной зоне того же порядка, что и в растянутой. Узких трещин всего в 1,5 раза больше, чем трещин с широким раскрытием. Случаев вырыва куска металла примерно в 2 раза меньше числа трещин с широким раскрытием. Во многих случаях разрушение произошло при остаточной деформации меньшей, чем допускаемая (0,8%).
В окрестности трещины металл во многих случаях слабо поврежден (микротрещины, цепочки пор).
Практически все гибы имели феррито-карбидную структуру металла.
Следует обратить внимание на то, что в пяти случаях разрушение гибов происходило с вырывом кусков металла. Это явилось результатом охрупчивания металла в процессе эксплуатации.
При анализе дополнительных данных из анкет — ответов на запросы по типовым формам — обращает на себя внимание малая доля демонтированных гибов, предварительно подвергнутых контролю. Так, из 3977 дефектных и подвергнутых замене гибов проконтролированы только 50% (1684). При этом обнаружены 484 гиба с микроповреждениями. Из 3977 всего 40 гибов демонтированы из-за превышения предельно допустимой остаточной деформации.
Таблица 1.15. Статистические данные по месторасположению и видам дефектов в металле замененных гибов из стали 12Х1МФ
Номер позиции | Месторасположение и вид дефекта | Зафиксированное |
1 | Растянутая зона | 37 |
2 | Нейтральная зона | 25 |
3 | Сжатая зона | 1 |
4 | Сквозные трещины | 48 |
5 | Несквозные трещины | — |
6 | Широкое раскрытие трещины | 11 |
7 | Узкое раскрытие трещин | 18 |
8 | Вырыв куска металла | 5 |
9 | Наличие сопутствующих трещин | 5 |
10 | Наличие цепочек пор | 5 |
11 | Наличие микротрещин | 19 |
12 | Тип структуры металла (феррито-карбидная) | 23 |
13 | Тип структуры металла (феррито-бейнитная) | — |
14 | Остаточная деформация > 0,8% | 3 |
Возможно, что многие гибы и на других ТЭС были демонтированы по истечении паркового ресурса и заменены на новые. Такую замену в современных условиях, по-видимому, следует считать неэффективной из-за больших материальных и трудовых затрат.
Например, в Свердловскэнерго есть опыт эксплуатации паропроводов в течение 250-400 тыс. ч, что существенно превышает их парковый ресурс. Следует подчеркнуть, что в данном случае в процессе эксплуатации проводили тщательный контроль рабочих параметров, а температура металла паропроводов не превышала 545 °C.
Статистический анализ по повреждениям гибов из стали 12Х1МФ проводился также на базе данных, включающей сведения ОС «Живучесть ТЭС», АО ОРГРЭС и УралВТИ [57]. Эта база насчитывает 124 случая разрушений гибов. Для них характерно наличие в гибах микро-, макро- и сквозных трещин.
Анализ, базирующийся на параметрической зависимости (1.12), выполнен по единой методике, включающей три взаимно согласованные формулы:
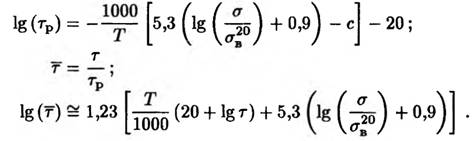
(1.33)
(1-34)
Здесь σ — p(Dном — s)/2s, T — температура металла, К; т — время наработки трубопровода, ч; тр — расчетное время до разрушения, ч; Dном — номинальный диаметр стенки трубы (гиба), мм; s — толщина стенки трубы (гиба), мм; р — давление, МПа;

При этом условием разрушения принято расчетное значение LM* — 20.
По данным табл. 1.16 были рассчитаны значения параметра т и построены графики дифференциального и интегрального распределения разрушенных гибов в зависимости от него (рис. 1.28).
Относительное количество разрушенных гибов v при дифференциальном распределении подсчитывалось по формуле:
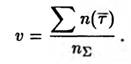
Относительное количество разрушенных гибов w при интегральном распределении определялось по формуле:
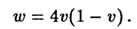
В формуле (1.35) величина n(т) — число разрушений при определенном значении LM*; n — общее число разрушений.
Приведенные на рис. 1.28 данные свидетельствуют о значительном разбросе времени до разрушения в окрестности т = 1. Примечательно, что только у 15% разрушенных гибов время до разрушения не превышает 0,5 от расчетного значения тр, а у 15% таких гибов время разрушения превышает удвоенное рассчитанное значение.
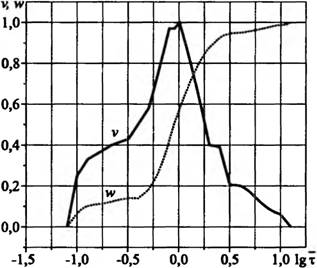
Рис. 1.28. Распределение разрушенных гибов паропроводов из стали 12Х1МФ: v — дифференциальное распределение; w — интегральное распределение
(1.36)
Таблица 1.16. Данные о разрушенных гибах паропроводов ТЭС и результаты их обработки
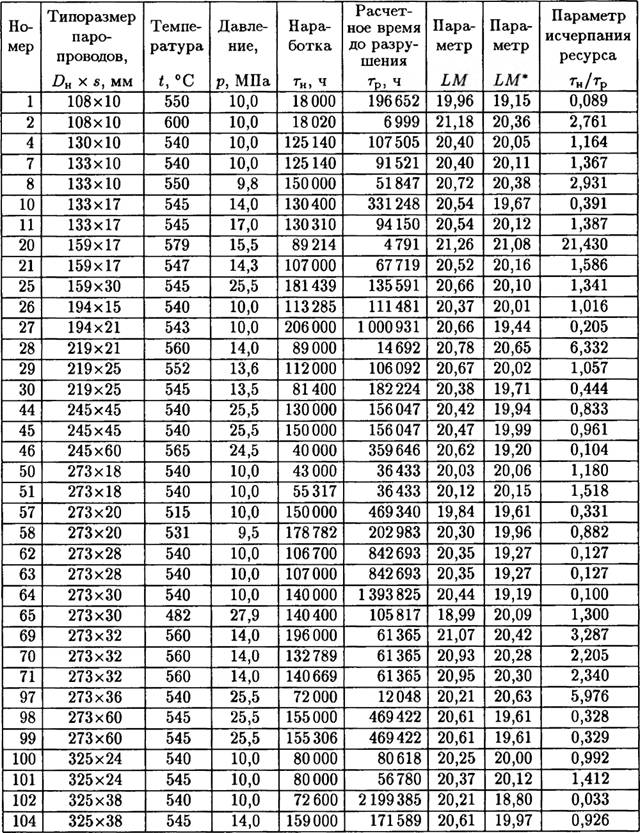
Рис. 1.29. Зависимость относительного количества различных повреждений гибов из стали 12Х1МФ от параметра LM*: 1 — все поврежденные гибы; 2 — гибы со сквозными трещинами; 3 — с микротрещинами; 4 — с цепочками микропор
На рис. 1.29 также представлены данные по разрушению и порообразованию в гибах из стали 12Х1МФ, имеющиеся в [57].
Кривая 1 на рис. 1.29 характеризует зависимость интегрального распределения w от параметра LM* для всех поврежденных гибов, кривая 2 — для гибов со сквозными трещинами, 3 — для гибов, имеющих микротрещины, и 4 — для гибов, имеющих цепочки пор, расположены кучно. Диапазон изменения LM* для этих кривых заключен в пределах 19,6 < LM* < 20,13, который значительно меньше диапазона для кривой 1.
Таблица 1.17. Зависимость доли исчерпания ресурса гибов т от параметра LM*
Таблица 1.18. Количество гибов паропроводов из стали 12Х1МФ, разрушенных и замененных по результатам контроля
Рис. 1.30. Количество гибов разрушенных nр и замененных по результатам контроля nэ, а также nр/n3 в зависимости от параметра LM*: 1 — n3; 2 — nр (сквозные трещины); 3 — nр/n3
Следует отметить, что средние значения и доверительные интервалы величины LM* для гибов с цепочками микропор, микротрещинами и сквозными трещинами, соответственно, равны: 19,997 ± 0,021; 19,951 ± 0,042; 19,975 ± 0,020. Эти значения перекрываются и сами по себе малоинформативны. Однако диапазон изменения LM* в этих условиях имеет величину ALM* ~ 0,03, т. е. такую же, как и для периода от образования цепочек микропор до снятия гиба с эксплуатации.
В том случае, если необходимо определить относительное время до разрушения гиба, т.е. долю исчерпания ресурса т — тп/тр, можно воспользоваться зависимостью т от параметра LM*, приведенной в табл. 1.17. Из этой таблицы следует, как было сказано выше, что с большой вероятностью разрушение можно ожидать при значениях LM* > 20.
В табл. 1.18 и на рис. 1.30 приведены зависимости количества разрушенных и замененных гибов из стали 12Х1МФ от параметра LM*. Примечательным является тот факт, что на основном диапазоне 19,5 < LM* < 20,3 отношение числа гибов со сквозными трещинами к числу гибов, замененных в результате контроля, существенно уменьшается при возрастании LM*. Гибы, для которых LM* > 20,4, практически отсутствуют, что хорошо иллюстрируется рис. 1.30. Интересно, что в диапазоне LM* < 20,3 интенсивность замены гибов по результатам контроля возрастает, а связанная с образованием сквозных трещин — заметно стабилизируется.
Таблица 1.19. Зависимость количества разрушенных гибов из стали 12X1 МФ от времени наработки
В табл. 1.19 и на рис. 1.31 приведены зависимости количества разрушенных гибов из стали 12Х1МФ от времени наработки. Эти данные свидетельствуют о том, что в области наработок 150-190 тыс. ч скорость нарастания числа разрушенных гибов существенно замедляется по сравнению с областью 80- 130 тыс. ч. Это, по-видимому, связано с тем, что в начале 70-х гг. на многих ТЭС произошло снижение температуры свежего пара с 565 до 545 °C, а также с тем, что в среднем диапазоне наработок прошла отбраковка гибов. При наработке 200 тыс. ч, очевидно, в эксплуатации преимущественно остались гибы с малой поврежденностью металла.
Рис. 1.31. Число разрушенных гибов паропроводов из стали 12Х1МФ в зависимости от наработки
Выводы
- Показана существенная информативность анализа числа замененных (по разным причинам) гибов.
- Скорость роста количества замененных и особенно внезапно разрушенных гибов замедляется в зависимости как от времени наработки, так и от обобщенного параметра LM*.
- Разрушения гибов из стали 12Х1МФ наблюдались преимущественно в растянутой зоне. Отмечены также случаи разрушения гибов в нейтральной зоне. Часть разрушений, особенно в нейтральной зоне, происходит при малой остаточной деформации (0,2-0,4%).
- Не отмечено ни одного случая разрушений гибов из стали 15Х1М1Ф. Однако, следует подчеркнуть, что сталь 15X1М1Ф обладает пониженной, по сравнению со сталью 12Х1МФ, длительной пластичностью, особенно, если металл имеет бейнитную структуру. Поэтому период от момента появления пор в металле до образования макротрещин может быть достаточно малым. Это необходимо учитывать при проведении эксплуатационного контроля и определении остаточного ресурса элементов паропроводов из стали 15Х1М1Ф.
- При тщательном индивидуальном контроле паропроводных гибов возможна их длительная эксплуатация сверх паркового ресурса.