Глава четвертая
ПРОИЗВОДСТВО СТЕКЛЯННЫХ ИЗОЛЯТОРОВ
1. СЫРЬЕВЫЕ МАТЕРИАЛЫ, ИХ ПЕРЕРАБОТКА И ПРИГОТОВЛЕНИЕ ШИХТЫ
Сырьевые материалы, используемые для производства стеклянных изоляторов, можно условно разбить на две труппы: основные и вспомогательные. Основные материалы: песок, сода, поташ, доломит, мел, глинозем — это тс, посредством которых в стекло вводятся основные стеклообразующие элементы и окислы. Вспомогательные: сульфат натрия, кремнефтористый натрии, плавиковый шпат — это материалы, введение которых в состав шихты диктуется необходимостью улучшить технологические свойства стекломассы.
Главным компонентом в составе стекол, используемых для выработки стеклянных изоляторов, является песок. С песком в стекло вводится основное количество SiO2. Для этих целей применяются пески трех месторождении: Новоселовского, Ташлинского и Великоглобовического. Пески поступают на заводы непосредственно с карьеров в необогащенном состоянии, поэтому одним из основных требований, предъявляемых к ним, является содержание кремнезема и постоянство химического состава. Пески указанных выше месторождении имеют состав, приведенный в табл. 4-1.
Таблица 4-1
Состав песков
♦ П. п. п. — потери при прокаливании.
Наличие в составе песка помимо кремнезема окислов различных металлов не играет особого значения, так как окиси кальция, магния и алюминия должны входить в состав стекла, а слабая окраска стекла за счет присутствия окиси железа и двуокиси титана заметно не влияет на свойства стеклянных изоляторов.
Окись натрия вводится в шихту в виде кальцинированной соды (Na2CO3) — порошкообразного гигроскопического материала белого цвета. Сода поступает на завод в закрытой таре и должна во избежание набухания храниться в сухом закрытом складе.
Окись калия вводится вместе с поташом (К3СО3). Поташ так же, как сода, поступает на завод в закрытой таре и тоже должен храниться в закрытом складе.
Через глинозем в стекло вводится окись алюминия. Обычно для производства стеклянных изоляторов используется технический глинозем марки ГА8 пли ГА85, который поступает па завод в обогащенном состоянии.
Окись кальция вводят в состав шихты в виде углекислого кальция СаСО3, для чего используется мел или известняк. В применяемом для производства стеклянных изоляторов материале содержание СаСО3 должно быть в пределах 95—98%. Кроме того, в состав мела, поставляемого на заводы непосредственно с карьеров, входят окиси железа и алюминия и в некоторых случаях углекислый магний (MgCO3).
Окись магния, а также окись кальция вводятся в виде доломита СаМg(СО3)2. Для производства стекла применяются доломиты различных месторождений (Ямское, Щелковское, Ннкитовское), по для выработки стеклянных изоляторов применяются только доломиты Орджоникидского месторождения, обладающие большим содержанием основных окислов СаО в MgO и лучшим постоянством химического состава.
Сульфат натрия Na2SO4 — химически чистый материал, поступает на завод в джутовых мешках, должен храниться в сухом закрытом складе. Он вводится в шихту в количестве 1% для улучшения осветления стекломассы, т. е. для освобождения стекла от газовых пузырей во время варки.
Эти же цели преследуются при введении в состав малощелочного стекла 2% фтора, который применяется пли в виде плавикового шпата CaF2, или в виде кремнефтористого натрия Na2SiF— белого порошка, изготовляемого из отходов суперфосфатного производства. Применение кремнефтористого натрия более предпочтительно, так как он в отличие от плавикового шпата является химически однородным материалом с постоянным составом. Кроме того, при его введении в состав шихты уменьшается потребность в соде. При варке стекла, особенно в пламенных печах, соединения фтора могут улетучиваться вместе с горячими газами. Это свойство фтористых соединений необходимо учитывать при расчете состава шихты.
Обязательным компонентом в составе стекломассы является возвратный стеклобой, который вводится в количестве 25—35% общего веса шихты. При этом очень важно сохранять постоянное соотношение свежей шихты и стеклобоя, а главное — применять стеклобой того же состава, что и основное стекло.
Все сырьевые материалы и возвратный стеклобой после соответствующей технологической обработки смешиваются по определенному рецепту и образуют шихту, пригодную для загрузки в стекловаренную печь.
Шихта должна иметь однородный состав. На однородность ее влияют размеры частиц, влажность, постоянного химического состава сырьевых материалов, способ и продолжительность перемешивания, транспортирование, хранение и загрузка. Все эти факторы необходимо учитывать при первичной обработке сырьевых материалов.
Установлено, что зерновой состав компонентов влияет на скорость стеклообразования, на способность шихты к расслоению, т. е. потерю структурной однородности. лучшими η этом отношении являются мелкозернистые пли пылевидные материалы. Чем мельче зерно основного компонента — кварца, тем более плотная упаковка всех остальных частиц материалов, входящих в состав шихты, тем активнее будет взаимодействие кварца с частицами плавней (окислами щелочных и щелочноземельных металлов) и тем быстрее будут протекать процессы стеклообразования. Уменьшение величины зерна кварцевого песка с 0,28 до 0,03 мм. повышает скорость стеклообразования почти в 10 раз. При подготовке сырьевых материалов необходимо соблюдать еще одно условие: чем крупнее зерно применяемого кварцевого песка, тем мельче должен дробиться мел или известняк.
Рис. 4-1. Сушильный барабан для сушки песка.
Очень важным показателем как исходных сырьевых материалов, так п готовой шихты является влажность. Влага в определенных пределах благоприятно влияет на качество шихты, так как увлажненное зерно кварца равномерно обволакивается другими компонентами, входящими в состав шихты. Такая композиция, состоящая из материалов с различными размерами и неодинаковыми удельными массами, не подвергается расслоению во время транспортировки и засыпки в печь.
Как указывалось выше, сырье для производства стеклянных изоляторов поступает на заводы навалом и в таре, в необогащенном состоянии и с гарантированным химическим составом. Необогащенное сырье, отгружаемое непосредственно с карьеров навалом (песок, мел, доломит), должно поступать на завод в чистых, закрытых, вагонах. Все материалы, прибывающие на завод, должны разгружаться только в определенные для этого вида сырья бункера и отсеки. Сырьевые материалы поступают в переработку после проверки лабораторией соответствия их требованиям государственных стандартов и технических условий. В зависимости от вида материала, сложности его доставки на завод, времени, необходимого для контроля его качества, на заводе должны создаваться запасы, обеспечивающие бесперебойную работу всего производства.
Технологическая обработка песка на заводе сводится к сушке, просеву и контролю качества. Чрезмерно влажный песок образует комки, которые затрудняют просеивание. Сушка песка производится в сушильном барабане (рис. 4-1).
Частота вращения барабана (в зависимости от типа) 3—8 об/мин. Теплоноситель — продукт сгорания природного газа. Песок при помощи питателя равномерными порциями подастся г. барабан. Температура в обогреваемой зоне сушильного барабана должна поддерживаться лётом в пределах 600 °C, зимой — в пределах 800 °C. В качестве дополнительного контроля может определяться температура отходящих из барабана газов, которая должна быть па уровне 120 °C. Песок после выхода из сушильного барабана должен иметь влажность не выше 0,02%. Высушенный песок для просева подастся ковшовым элеватором на вибрационное или роторное сито № 08. Просеянный лесок направляется в расходные бункера. Отсев, содержащий крупные фракции и посторонние примеси, направляется в отвал. Перед загрузкой песка в расходные бункера его желательно подвергнуть магнитной сепарации.
Доломит перед использованием подвергается дроблению, сушке, окончательному помолу и просеву. Дробление доломита производится в щековой дробилке до величины кусков 35—50 мм, после чего он подается на сушку. Сушка осуществляется в сушильном барабане при температуре газов в обогреваемой зоне не выше 400 °C, так как при более высокой температуре доломит начинает диссоциировать. Температура отходящих газов в этом случае будет находиться па уровне 80 °C. Высушенный доломит подастся системой элеваторов и транспортеров для окончательного измельчения на бегуны, затем в шаровую или молотковую дробилку. Наиболее тонкое и равномерное измельчение достигается в шаровой мельнице, по производительность этого вида оборудования несколько ниже, чем молотковых дробилок. Наиболее прогрессивным оборудованием для измельчения сырьевых материалов, применяемых в стекольном производстве, необходимо признать аэробильные мельницы, в которых совмещены помол, сушка и сепарация материала. В такой мельнице куски материала подаются в разгонную трубу, где они подхватываются потоком горячих газов и, ударяясь о специальную плиту, измельчаются.
Измельченный материал подвергается разделению на фракции, причем грубые фракции возвращаются на домалывание.
Высушенный и измельченный доломит подвергается разделению на фракции при помощи № 0,9—№ 11 либо при помощи сепаратора.
Разгрузка доломита из шаровой мельницы и подача его в расходный бункер могут осуществляться с использованием пневмотранспортера (рис. 4-2). Молотый материал поступает в сопло, куда одновременно поступает воздух, засасываемый вентилятором. Образующаяся в сопле пылевоздушная смесь направляется в сепаратор, где крупные частицы материала отделяются и возвращаются в бункер, питающий шаровую мельницу. Мелкие, же фракции направляются в циклон, где вследствие центробежной силы и резкого падения скорости материал отделяется от воздуха и попадает в расходный бункер. Окончательная влажность доломита перед загрузкой его и расходный бункер не должна превышать 0,04%.
Технология обработки мела идентична технологии обработки доломита и осуществляется на том же самом оборудовании. Иногда помол крупных фракции мела производится па дезинтеграторах, которые отличаются от прочего мелящего оборудования способностью перерабатывать материалы с большей степенью влажности.
В том случае, когда технологическая линия обработки мела совмещена с линией обработки доломита, все оборудование при переходе с одного вида материала на другой должно подвергаться тщательной очистке.
Рис. 4-2. Схема пневмоподачи доломита и мела в расходный бункер.
Влажность мела перед загрузкой его в расходный бункер должна быть не выше 0,04%. При контрольном просеве мела через сито № 08—№ 1 не должно оставаться остатка.
Такие материалы, как сода, поташ, сульфат натрия поступают на завод в закрытой таре, поэтому никакой очистке не подвергаются. Из мешков эти материалы с помощью элеваторов или вакуумной системы подаются на сита № 08—09 и оттуда в расходный бункер. Так как эти материалы чрезвычайно гигроскопичны, то они подвержены комкованию при хранении и транспортировке.
Отсеиваемые на сите комки соды или поташа направляются в дезинтеграторы, а оттуда — на повторный просев. Также не требуют никакой обработки, кроме просева, кремнефтористый натрий и технический глинозем. Первый просеивается через сию № 1, 6, а второй — через сита № 08—№ 09. Влажность кремнефтористого натрия, предназначенного для производства, должна быть не более 1%, допустимая влажность глинозема 3%.
Стеклобой со склада хранения в контейнерах подается на дробильную установку. Как правило, дробление осуществляется с помощью щековой дробилки до величины кусков 35—50 мм. Применяемый для приготовления шихты стеклобой должен быть очищен от грязи и всевозможных посторонних предметов. Готовый стеклобой, пропущенный через магнитный сепаратор, хранится в расходном бункере.
Подготовленные таким образом сырьевые материалы используются для приготовления шихты.
Приготовление шихты — взвешивание и смешивание всех исходных сырьевых материалов и стеклобоя — является очень ответственной операцией, от соблюдения режимов которой зависит в значительной степени качество стекломассы и готовых стеклянных элементов изоляторов.
Как правило, все компоненты, входящие в состав шихты, взвешиваются на автоматических весах, устанавливаемых под каждым расходным бункером и отвешивающих заданные порции материалов с заданной периодичностью.
В цехах изоляторных заводов используются автоматические весы типов ДСТ-70; ДП-20; ДСМ-20-50. Автоматические весы могут быть объединены в линии взвешивания, работающие в автоматическом режиме. В зависимости от порции отвешиваемого материала в этом случае используются весы различных типов. Так, для песка устанавливаются весы типа ДВСТ-300 (единовременная навеска до 300 кг), для взвешивания доломита — весы ДВСТ-150, поташа и мела ДВСТ-40, сульфата — ДВСТ-10. Все весы снабжены циферблатными головками со стрелочными указателями. На циферблатах размешены электронные бесконтактные датчики пределов, сигналы от которых подаются на панели управления. Органы централизованного автоматического управления весами всей линии концентрируются на общем пульте, располагаемом в пультовом помещении. Оператор может судить о работе отдельных весов и всей линии в целом по световым сигналам мнемосхемы. Загрузка и разгрузка материалов на линии может производиться автоматически по заданной циклограмме. Взвешенные материалы через вибропитатели поступают на транспортер и дальше — в смеситель.
На всех весах предусмотрена блокировка, исключающая возможность выгрузки на транспортер материалов в случае неправильной дозировки. В тех цехах, где количество приготовляемой в сутки шихты не требует создания автоматических линий взвешивания, могут применяться либо стационарные весы, либо подвижные весы, устанавливаемые на тележке или монорельсе. Такие весы производят поочередное взвешивание каждого из компонентов. Естественно, что при работе на таких весах возможны ошибки, связанные с субъективными качествами обслуживающего персонала.
Отвес каждой порции материалов, подлежащих дальнейшему смешиванию, необходимо производить только в соответствии с рецептом, выданным лаборантом данной смены после проверки лабораторией всех сырьевых материалов на качество просева, влажность и содержание основного вещества.
Все исходные материалы должны подаваться в смесители в строго определенном порядке. Например, при смешивании материалов для варки щелочного стекла они подаются в смеситель в следующей последовательности: песок, доломит, сульфат натрия, глинозем, поташ, мел, сода. Приготовление шихты малощелочного стекла осуществляется в другом порядке: песок, кремнефтористый натрий, глинозем, доломит, мел. Так как шихта должна обладать определенной влажностью (2—5%), то песок перед смешиванием с остальными компонентами подвергается увлажнению непосредственно в смесителе с помощью установленных там форсунок. При этом влага равномерно распределяется вокруг зерен песка, образуя водяную пленку.
Рис. 4-3. Тарельчатый смеситель шихты.
После увлажнения, которое продолжается около 3 мин, в смеситель подаются в указанной последовательности остальные материалы, обволакивающие в процессе смешивания увлажненные зерна кварца, что обеспечивает повышенную реакционную способность шихты и закрепляет взаимное расположение частиц материалов. Исключение составляет шихта, предназначенная для варки малощелочного стекла 13в в электрической печи. Исходя из специфических условий электроварки этого стекла, специальное увлажнение шихты не производится. В этом случае влажность шихты, которая не должна превышать 2%, достигается за счет естественной влажности составляющих материалов. Сырьевые материалы смешиваются в течение 5—10 мин.
В том случае, когда шихта и стеклобой загружаются в стекловаренную печь одновременно, что является наиболее предпочтительным вариантом, в смеситель после смешивания шихтовых материалов подается стеклобой и смешивание продолжается еще некоторое время.
Рис. 4-4. Роторный смеситель шихты.
Для приготовления шихты на изоляторных заводах используются два типа смесителей: тарельчатый и роторный. Тарельчатый смеситель (рис. 4-3) состоит из вращающейся на роликах тарелки, на которую подаются сырьевые материалы, и механизма перемешивания, включающего в себя лопасти и катки, расположенные эксцентрично по отношению к осп тарелки и вращающиеся от самостоятельного привода.
Благодаря такому сложному движению частицы материалов совершают спиралеобразный путь, что обеспечивает тщательное перемешивание и усреднение шихты. Однако тарельчатый смеситель — это смеситель открытого типа, поэтому при засыпке и перемешивании очередных порций материалов неизбежно пыление и небольшая потеря некоторых компонентов. Этот недостаток отсутствует в смесителе роторного типа (рис. 4-4). Перемешивание материалов в роторном смесителе производится в закрытом барабане, имеющем специальные лопасти.
В готовой шихте допускаются некоторые отклонения, как по массе исходных материалов, так и по содержанию основных окислов. Так, например, содержание песка может колебаться в пределах 1% мела, известняка, соды, сульфата натрия и доломита 0,5%. В зависимости от допустимых отклонений в содержании основных окислов шихта делится па три сорта. Например, сортность шихты малощелочного стекла определяется следующими допустимыми отложениями отклонениями от рецептуры:
Шихта с отклонениями, превышающими указанные, бракуется и не допускается к загрузке в стекловаренную печь.
Хранение и подача готовой шихты в печь осуществляются обычно в специальных металлических контейнерах-кюбелях. Приготовление и подача шихты к загрузочному карману печи должна осуществляться небольшими порциями. Во избежание слеживания и высыхания шихта после приготовления должна храниться не более 8—10 ч. Чтобы не допустить расслоения шихты, необходимо создать такие условия ее транспортирования, которые исключают свободное падение шихты с большой высоты, встряхивание и вибрацию при перемещении кюбелей. Соблюдение всех этих требований позволяет получить шихту требуемого качества с высокой степенью однородности.
На рис. 4-5 приведена примерная схема обработки материалов и приготовления шихты малощелочного стекла.
В последнее время в стекольной промышленности используются и другие способы транспортирования шихты к печам. Пневматическая подача шихты из смесителя в загрузочное устройство печи создает благоприятные условия применения свежеприготовленной шихты и не требует изготовления многочисленного парка кабелей. Однако этот метод не исключает полностью расслоения шихты при транспортировке. Стабильная однородность и полное отсутствие расслоения достигаются при брикетировании шихты. Брикетирование шихты помимо указанных преимуществ исключает запыление цехов и регенераторов печей, позволяет создать запасы шихты на несколько дней или даже недель. Брикетирование шихты осуществляется в специальных прессах на вальцах или таблетмашинах.
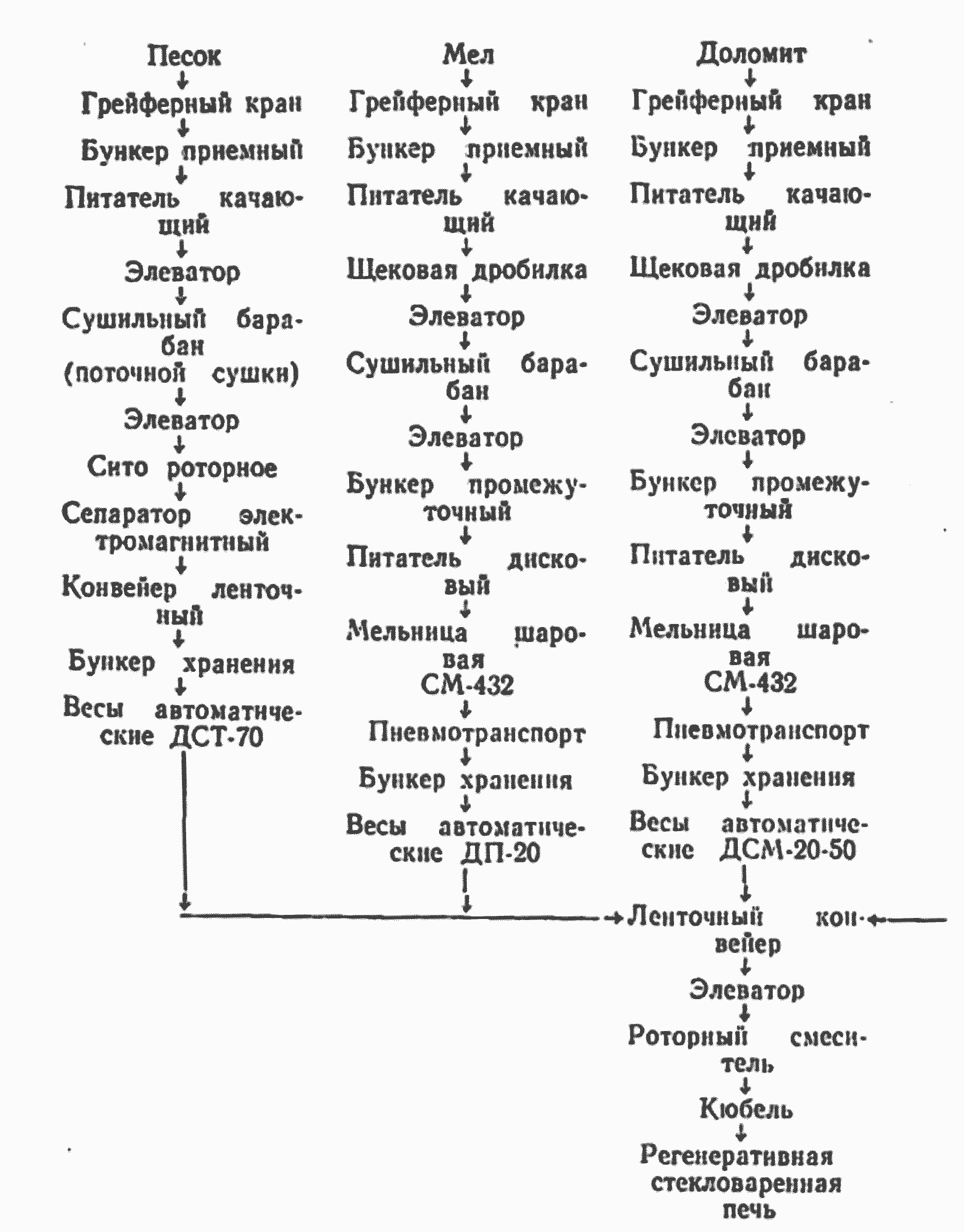
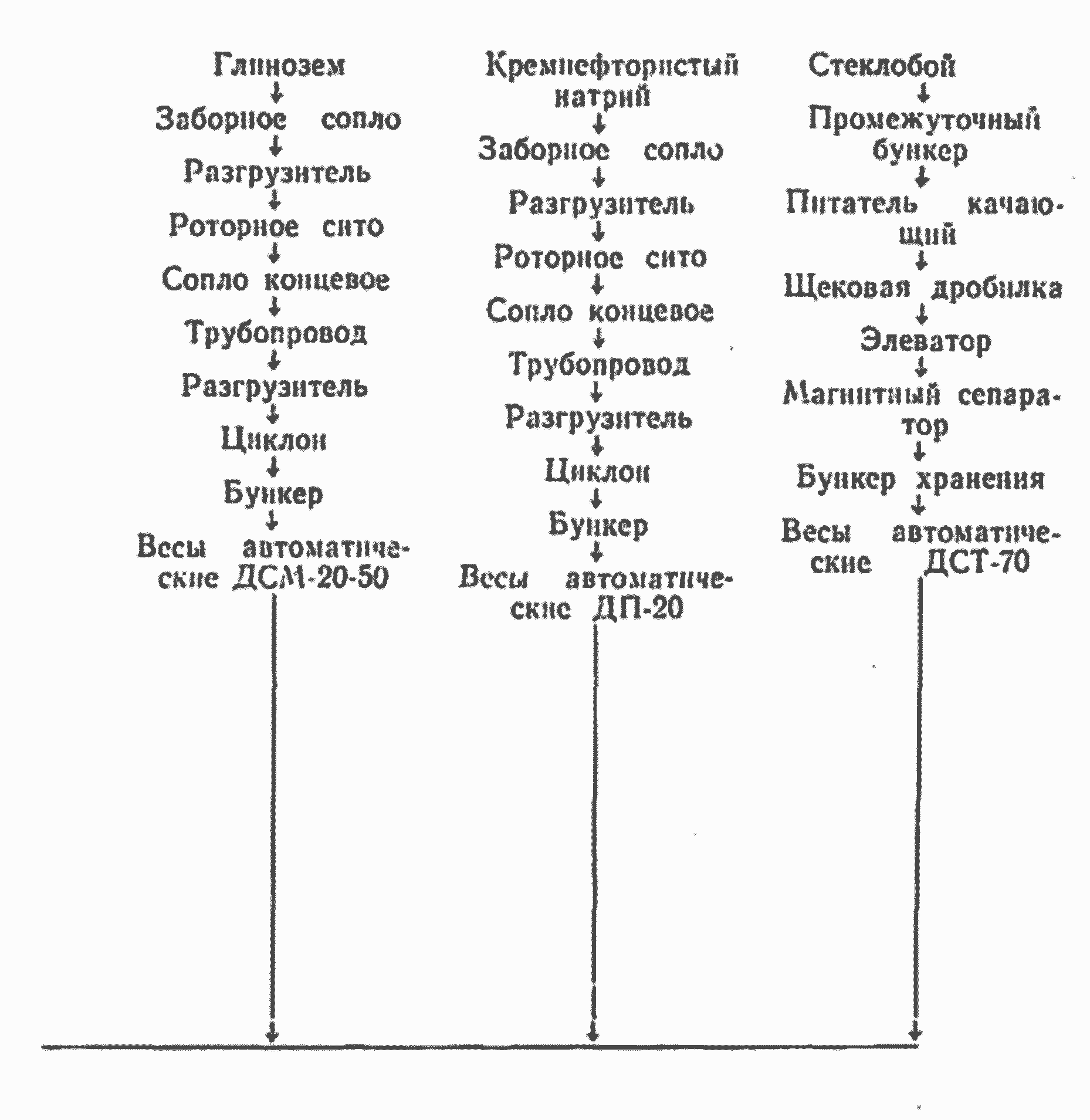
Рис. 4-5. Технологическая схема приготовления шихты.
Для улучшения условий формовки брикетов в шихту добавляют в качестве связующего жидкое стекло. Готовые брикеты подвергаются сушке при температуре 200 °C. Подача брикетов к печам может осуществляться любым видом транспорта и в любой таре.