Коллекторы.
В процессе длительной работы у машин постоянного тока повреждается чаще всего коллектор: нарушается его геометрически правильная форма, происходят замыканий коллекторных пластин, выступает межпластинная изоляция над пластинами, изнашиваются и оплавляются пластины коллектора.
Рис. 116. Переносные приспособления для проточки (а) и шлифовки (б) коллектора при вращении якоря машины постоянного тока в собственных подшипниках:
1 — станина, 2 — суппорт, 3 — резец, 4 — карборундовый круг . 5 — гибкий вал, б — электродвигатель.
Нарушение геометрически правильной формы коллектора происходит чаще всего из-за неудовлетворительной эксплуатации машин и, главным образом, несвоевременного продороживания коллектора. Неисправность характеризуется образованием волнистости на рабочей поверхности коллектора вследствие неравномерного износа его пластин в продольном направлении и повышенным радиальным биением.
Чтобы устранить дефект, восстановить правильную геометрическую форму и создать требуемую шероховатость поверхности, коллектор обтачивают на токарном станке, а затем шлифуют и полируют. Для получения коллектора правильной геометрической формы следует тщательно выверить вал (при установке якоря на станке) по его шейкам предварительно рейсмасом, а затем индикатором. Обточку коллектора производят при минимальной подаче (не более 0,05 мм/об) резцами с пластинами, из твердого сплава ВК-6 или ВК-8, со скоростью резания 1 — 1,5 м/с, не превышающей номинальной рабочей окружной скорости коллектора. При обточке следует снимать с коллектора столько металла, сколько необходимо для устранения дефекта.
По окончании обточки коллектор продороживают, а затем шлифуют и полируют. В ремонтной практике обточку и шлифовку производят с помощью переносных приспособлений (рис. 116, а, б) при вращении якоря машины в собственных подшипниках. Шлифовку коллектора выполняют при номинальной частоте вращения якоря. Полировку — с помощью деревянных брусков из несмолистых пород древесины (бук, клен), которые вставляют в щеткодержатели вместо щеток так, чтобы их волокна были расположены перпендикулярно к коллектору. Полировка способствует более быстрому образованию на поверхности коллектора оксидной пленки («политуры»), необходимой для хорошей коммутации.
Рис. 117. Приспособления для продороживания коллекторов машин постоянного тока: а — ручной резак, б — переносное устройство для механической выборки межпластинной изоляции коллектора; 1 — электродвигатель, 2 — магнитный пускатель, 3 — редуктор, 4 — карданный валик, 5 — рукоятки, 6 — рабочая часть
Ремонт коллектора завершается продороживанием, заключающимся в прорезании межпластинной миканитовой изоляции на глубину 0,5 —1,5 мм в зависимости от размеров коллектора.
При небольшом числе ремонтируемых машин постоянного тока продороживание коллекторов производят ручными резаками (рис. 117, а) с вставленными в них отрезками ножовочного полотна, а на ремонтных предприятиях — с помощью специального переносного устройства ПМР-20К (рис. 117,6), состоящего из электродвигателя и рабочей части с фрезой. Электродвигатель 1 мощностью 0,25ккВт снабжен редуктором 3 с передаточным числом 1: 3. Управление двигателем осуществляется магнитным пускателем 2, "кнопка включения и отключения которого размещена в правой рукоятке 5 рабочей части б. Рабочая часть снабжена метрической шкалой для установки дисковых фрез на размер и шаг коллекторных пластин, а также концентрическим зажимом, позволяющим регулировать глубину продороживания. Прорезание изоляции осуществляется фрезой левого вращения и соответствующей толщины.
Продороживание выполняют следующим образом. Заземляют электродвигатель и подключают его к сети. Устанавливают при помощи каретки и подвижных опор необходимую глубину продороживания и шаг коллекторных пластин. После этого вручную продороживают первую прокладку между пластинами. Затем, взяв в руки рабочую часть приспособления, ставят направляющий нож в продороженную канавку, пускают двигатель и, направляя вращающуюся фрезу вдоль изоляционной прокладки между пластинами, продороживают ее. Нажимают кнопку и останавливают электродвигатель, устанавливают направляющий нож в только что выбранную фрезой дорожку и, повторяя операцию, выбирают фрезой следующую дорожку между пластинами коллектора.
Переносное устройство для продороживания изоляции коллектора широко используют в ремонтной практике, поскольку снижаются затраты труда на эту операцию в 6 раз по сравнению с выполнением вручную и намного повышается качество продороживания.
Приступая к работе по продороживанию, необходимо убедиться в правильности направления вращения фрезы (с помощью стрелки, прикрепленной на корпусе устройства) и прочности ее крепления. Работу по продороживанию. выполняют в защитных очках, в одежде, рукава которой должны быть завязаны на запястьях рук.
По окончании продороживания края пластин обрабатывают напильником (снимают заусенцы) и скашивают под углом 45°, как показано на рис. 118. В ряде случаев у коллектора могут оказаться поврежденными пластины настолько сильно, что без их замены его дальнейшая работа невозможна. Наиболее частой причиной повреждения коллектора является возникновение на его поверхности множества электрических разрядов (электрических дуг), распространяющихся по поверхности и образующих «круговой огонь», что объясняется очень высоким (обычно более 20 В) напряжением между смежными пластинами коллектора. Интенсивность образования и перехода мелких электрических разрядов в круговой огонь зависит от параметров электрической машины и, в первую очередь, ее мощности, активного сопротивления и индуктивности секций, а также частоты вращения якоря.
У машин небольшой мощности образование кругового огня приводит к появлению следов почернения на поверхности коллектора, а у крупных машин — мощных коротких дуг, вызывающих частичное оглавление кромок смежных пластин и образование прожогов (кратеров) глубиной до 2 мм.
Техническими условиями Главэнерго ремонта Минэнерго на ремонт электрических машин постоянного тока допускается замена до пяти пластин коллектора ремонтируемой машины. Замену поврежденных пластин производят при помощи специальных приспособлений с соблюдением мер,
Рис. 118. Обработка пластин и выборка межпластинной изоляции при продороживании коллектора
Рис. 119. Замена поврежденных пластин коллектора при помощи специального приспособления:
1 — гайка, 2 — шайба, 3 — диск, 4 — отпаянные провода, 5 — стяжная шпилька, б — вырез для удаления пластин, 7 - пластины коллектора; Z t и / 2 — диаметры коллектора и петушков
обеспечивающих сохранение монолитности и геометрической формы коллектора.
Поврежденные* пластины заменяют с помощью приспособления (рис. 119) следующим образом. Снимают бандаж, отпаивают провода обмотки якоря от петушков и отгибают их так, чтобы они не мешали дальнейшим операциям ремонта. Устанавливают ремонтный диск 3 приспособления, имеющий специальный вырез 6, размер которого равен размеру рядом находящихся и подлежащих замене пластин; диск устанавливают и закрепляют стяжными шпильками 5, чтобы его вырез оказался напротив заменяемых пластин. Далее снимают нажимное кольцо (шайбу 2) и миканитовую манжету коллектора и при помощи зубила и. молотка сдвигают пластину вдоль оси коллектора до выхода ее «ласточкина хвоста» из конусного выступа втулки, а затем перемещают пластину в радиальном направлении и извлекают ее из коллектора.
*Для облегчения снятия миканитовой манжеты коллектор нагревают до 70—80 °С.
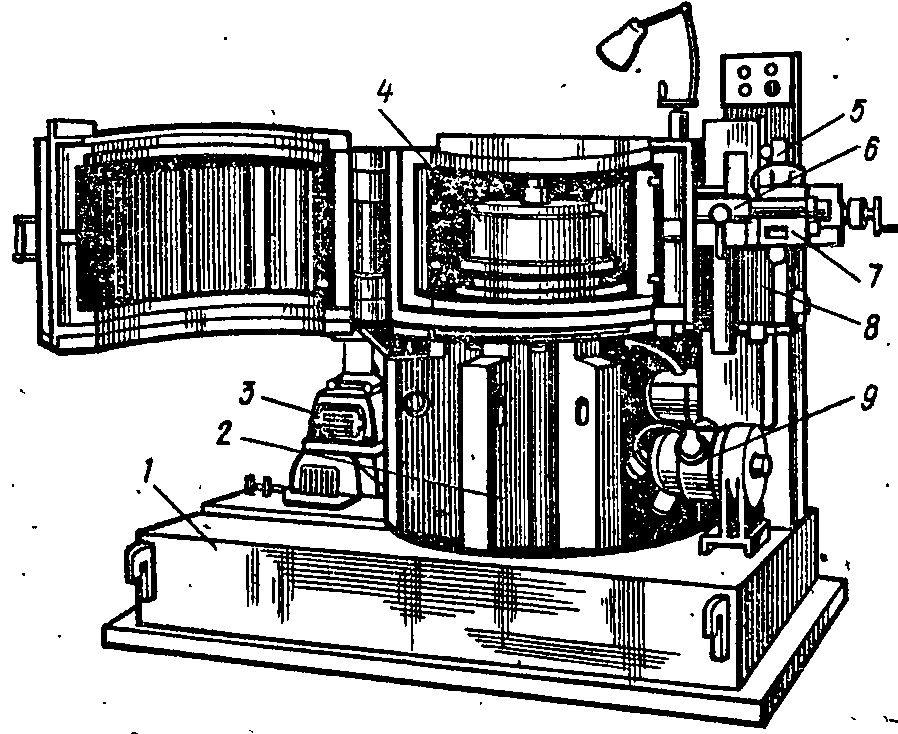
Рис. 1.20. Станок для динамической формовки коллекторов:
1 — станина, 2 и 3 опорная колонна и привод шпинделя, 4 — нагревательная камера, 5 — ходовой винт, 6 — поворотная головка, 7 — каретка, 8 — механизм суппорта проточки, 9 — пылесосное устройство
Новые пластины должны быть изготовлены из тех же материалов и иметь такой же профиль и размеры, как и заменяемые поврежденные пластины. Их предварительно собирают и спрессовывают с миканитовой изоляцией и между собой, а затем устанавливают в коллекторе.
Сборку коллектора производят в последовательности, обратной разборке. После - ремонта с заменой одной, или нескольких пластин коллектор формуют. На хорошо оснащенных оборудованием крупных электроремонтных заводах для динамической формовки коллекторов применяют специальные станки (рис. 120).
Станок состоит из станины 7, размещенных на ней опорной колонны 2 шпинделя, привода 3 шпинделя, нагревательной камеры 4, механизма 8 суппорта проточки и пылесосного устройства 9.
Нагревательная камера 4 состоит из двух шарнирно соединенных частей, одна из которых неподвижна, а. другая открывается при установке и снятии коллектора. Нагревается Камера с помощью трубчатых электронагревателей, размещенных между внутренней и наружной стенками и изолированных от них теплозащитной изоляцией. Заданная температура в камере поддерживается автоматически терморегулятором. Пылесосное устройство служит для удаления медной и миканитовой стружки.
Коллектор, подлежащий разгону, устанавливают на шпиндель и закрепляют гайкой. Шпиндель приводится во вращение электродвигателем через клиноременную передачу.
1 - вороток, 2 — винт, 3 - диск, 4 - коллектор, 5 — крюк
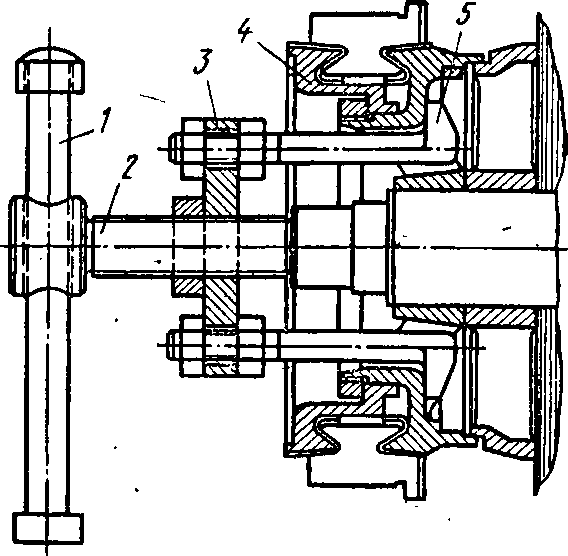
Рис. 121. Приспособление для снятия коллектора с вала якоря:
Суппорт, предназначенный для проточки контрольного пояска, имеет две рабочие подачи: продольную — Вертикальное перемещение по направляющим стойки при помощи ходового винта 5 и поперечную — горизонтальное перемещение по направляющим каретки 7. На каретке установлена поворотная головка 5, имеющая два держателя: один — для закрепления резца для проточки пояска, другой — для бесконтактного датчика установки контроля геометрической формы коллектора (на рисунке не показан). Суппорт при проточке пояска перемещают вручную с помощью винтовой подачи, при этом резец врезается в коллектор на определенную глубину. Продольную подачу суппорт с резцом получает от электродвигателя через редуктор, коническую пару шестерен, червячную передачу и ходовой винт. Он имеет ускоренное продольное перемещение, осуществляемое с помощью обгонной муфты, получающей вращение от первой ступени редуктора при включении электромагнитной муфты.
При использовании станка обеспечиваются высокое качество формовки коллектора и эксплуатационная надежность работы электрической машины.
При большом числе поврежденных пластин коллектор снимают с вала при помощи- приспособления (рис. 121), предварительно отсоединив концы обмотки якоря от пластин или петушков. Чтобы снять коллектор, вводят в вентиляционные каналы коллектора 4 шесть крюков 5 и поворачивают их на 90°, чтобы они захватывали корпус коллектора. Концы крюков вставлены в отверстия диска 3. В центре диска нарезана резьба для винта 2. Вращая винт воротком /, стягивают коллектор с вала якоря. Взамен снятого устанавливают новый коллектор заводского изготовления. Замене подлежат также коллекторы, износ пластин которых по толщине составляет: при диаметре коллектора до 100 мм — 2,5; 150— 200 мм — 3,5; 250 — 500 мм — 5 мм.
Щеточный аппарат. Этот аппарат электрической машины состоит из щеткодержателей со щетками и щеточных пальцев, собранных на поворотной траверсе. В коллекторных машинах применяют в основном два вида щеткодержателей: радиальные и реактивные (наклонные).
Радиальные щеткодержатели (см. рис. 107,б) характерны тем, что ось щетки направлена по радиусу коллектора. Давление на щетку 5 создается пружиной 3 и передается через рычаг 2 и пружину 8, которая служит буфером. Верхний конец пружины 8 шарнирно соединен с рычагом 2, в нижний ее конец ввернут на резьбе фарфоровый наконечник 7, который вставляют в углубление, просверленное в щетке 5.
Фарфоровый наконечник препятствует переходу тока через стальную пружину, что могло бы вызвать ее нагрев и нарушить упругость вследствие отпуска стали, Щетка вставлена в обойму б, которая отлита из латуни и прикреплена к корпусу 4 щеткодержателя, представляющему собой штампованную коробочку из листовой стали. Конец щеточного пальца Закрепляют в хомутике траверсы.
Радиальные щеткодержатели применяют в реверсивных электрических машинах, где якорь вращается с переменной направления вращения. В электрических машинах, вращающихся постоянно в. одном направлении, используют реактивные (наклонные) щеткодержатели (см. рис. 107, г), у которых щетка наклонена по отношению к радиусу коллектора по его ходу. При этом щетка 11 прижимается к стенке 12 обоймы пружиной 15, которая регулируется храповиком 13, запираемым пружинным штифтом 10, и не опрокидывается. Конец пружины 15 согнут в колечко 14 и играет роль нажимного рычага. Ток от щетки отводится по гибкому проводу, сплетенному из тонких медных нитей, к пальцу щеткодержателя.(Щеткодержатель надевается на палец щеточного устройства и удерживается на нем разрезным хомутиком 9. Этот щеткодержатель называется реактивным, поскольку щетка находится под действием реакций двух сил.
В синхронных и асинхронных электрических машинах применяют щеткодержатели зажимного Типа, у которых щетки не скользят в обойме, а зажаты в корпусе щеткодержателя и при износе опускаются вместе с ним. Корпус щеткодержателя может быть выполнен из штампованных деталей без механической обработки.
Обычно щеткодержатели зажимного типа (рис. 122) выполняют сдвоенными — на одном пальце. 1 над каждым контактным кольцом располагаются две щетки 5. Каждая щетка стопорным винтом 4 зажата в корпусе 3 щеткодержателя и прижимается к контактному кольцу пружиной б. Корпуса Щеткодержателей шарнирно соединены с хомутиком 2. По мере износа щеток и контактных колец величина нажатия щетки на контактное кольцо не изменяется, поскольку с уменьшением длины плеча пружины увеличивается сила нажатия пружины.
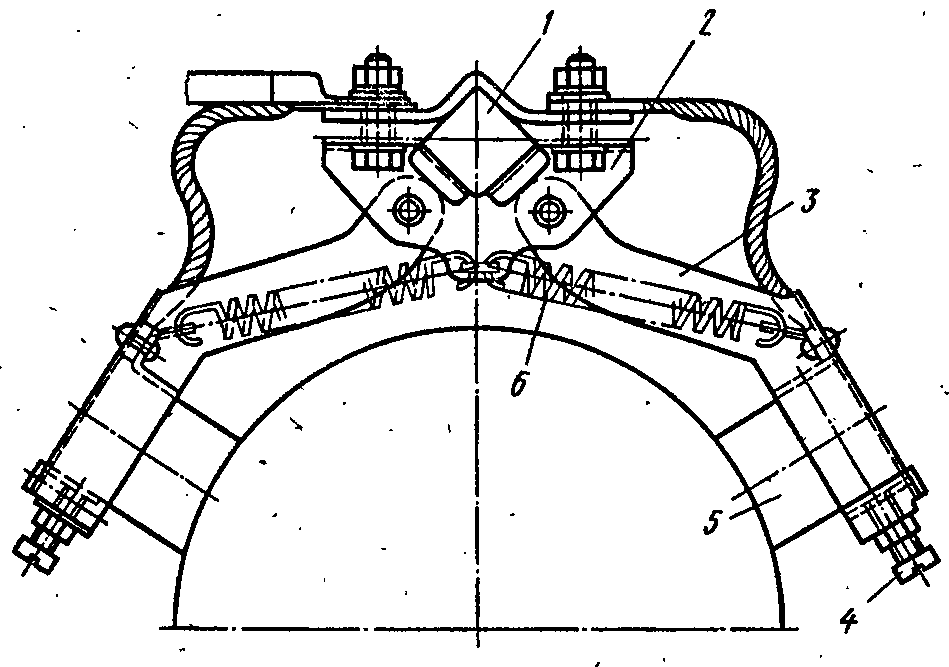
Рис. 122. Щеткодержатель зажимного типа синхронных и асинхронных машин
В машинах постоянного тока из-за ограничения величины перекрытия коллекторные пластин щетки располагают узкой стороной вдоль окружности коллектора. В асинхронных машинах щетки узкой стороной направляют вдоль контактных колец, благодаря чему уменьшают их ширину. В машинах постоянного тока щеткодержатели одинаковой полярности укреплены на неизолированном металлическом пальце, а и асинхронных машинах щеткодержатели контактных колец, относящихся к разным фазам, — на изолированном пальце,
При ремонте электрических машин наиболее часто встречаются такие неисправности щеткодержателя, как ослабление пружин, оплавление или механические повреждения.
Ослабление пружин щеткодержателя,- следовательно,- снижение нажатия на щетку устраняют регулировкой пружин, а при отсутствии такой возможности — заменой дефектной пружины новой заводского изготовления. Величину нажатия пружины щеткодержателя после регулировки или замены проверяют самым доступным способом, показанным на рис. 123. Величина нажатия щеток зависит от их марки, конструкции машины и др.
Величину нажатия щеток 3 на коллектор 1 определяют так: подкладывают под щетку на коллектор полоску бумаги или фольги), затем одновременно тянут одной рукой за шнурок, привязанный к крючку динамометра, а другой — за бумагу и замечают показание динамометра в момент, когда бумагу можно легко вытянуть из-под щетки. Удельное нажатие определяется как частное от деления величины, показанной динамометром в граммах, на поперечное сечение щетки в
квадратных сантиметрах. Отклонения в усилии нажатия отдельных щеток одного полюса машины постоянного тока не должны превышать 10%. Все щетки, устанавливаемые на отремонтированной машине, должны быть одной марки. Марки щеток подбирают в соответствии с указаниями завода-изготовителя, так как каждый тип машины выпускается заводом со строго подобранными марками ще- ток. При подборе щеток учитывают плотность тока под ними, окружную скорость коллектора или контактных колец, род тока и напряжение, мощность электродвигателя и режим его работы.
1 — коллектор, 2 — щеткодержатель, 3 — щетка, 4 — динамометр, 5 — нажимной палец, 6 — пружина,
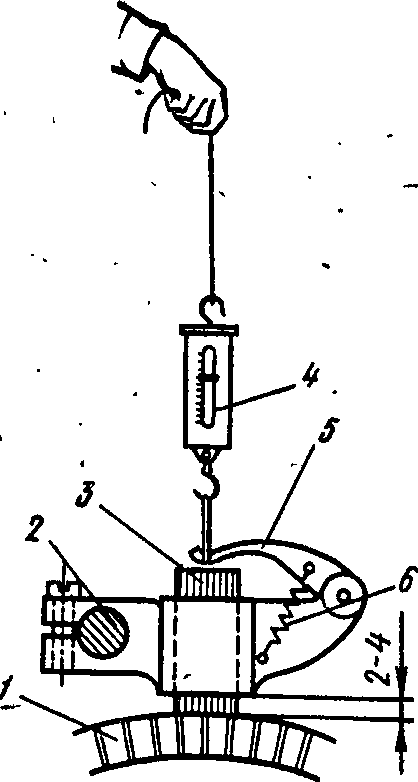
Рис. 123. Проверка величины нажатия пружины щеткодержателя:
Правильный подбор удельного нажатия и марки щеток способствует улучшению контакта между щетками и коллектором, однако этого недостаточно для создания надежного и хорошего контакта. Необходимо, чтобы контактные поверхности щеток были тщательно притерты (пришлифованы) к поверхности коллектора.
Для этого устанавливают щетку 3 (см, рис. 123) в держатель 2, а затем, приподняв ее, накладывают полоску стеклянной бумаги "на поверхность коллектора 1 (абразивной поверхностью к щетке) и опускают щетку. Для пришлифовки щеток применяют только мелкозернистую стеклянную бумагу № 00, Прижимая бумагу к поверхности коллектора и держа за концы, протягивают ее от одного крайнего положения до другого до тех пор, пока щетка не притрется. Притерев каждую щетку, таким же способом притирают одновременно группу щеток одного щеточного пальца или одной полярности.
Обоймы и другие детали щеткодержателя оплавляются из-за сильного искрения и реже от образования кругового огня. При легком оплавлении щеткодержатель очищают от копоти грязи и нагара, а, при сильном — заменяют новым. Механические повреждения щеткодержателя (заусенцы, вмятины, выгибы) устраняют опиловкой и правкой. Повреждением, часто встречающимся в щеткодержателях, является электрическая коррозия внутренней поверхности обоймы в результате нарушения прохождения тока с щетки на обойму. Неисправность устраняют -подтяжкой контактов в цепи тока, сильно коррозированную обойму заменяют.
Окончив ремонт щеткодержателей и притирку щеток машин постоянного тока, проверяют правильность сборки и расстановку щеткодержателей по отношению к коллектору. Эту работу выполняют очень тщательно, так как малейшее изменение порядка расстановки щеткодержателей или несоблюдение расстояний от щеткодержателей до коллектора может привести к нарушению нормальной работы машины и повышенному износу коллектора и щеток. Правильной является такая расстановка щеток, при которой щетки равномерно расположены на рабочей поверхности коллектора.
При расстановке щеток учитывают, что износ коллектора под щетками разной полярности неодинаков. Поэтому щеткодержатели располагают так, чтобы щетки двух соседних болтов разной полярности работали по одному щеточному следу, а следующей пары болтов — по другому следу, т. е. в промежутках между щеточными следами первой пары болтов. Устанавливая щеткодержатели, следят, чтобы расстояние от обоймы до поверхности коллектора было 2—4 мм. Для свободного передвижения щеток в обоймах между ними должен быть зазор 0,1—0,4 мм в направлении вращения и 0,2— 0,5 мм — в направлении оси коллектора.
Контактные кольца. В асинхронных двигателях с фазным ротором применяют два вида контактных колец: с коротко- замыкающим устройством и без короткозамыкающего устройства (с постоянно налегающими щетками на контактные кольца). Электродвигатели с короткозамыкающим устройством использовались в электродвигателях, выпускавшихся до 1940 г. Такие двигатели в небольшом количестве все еще эксплуатируются и поступают в ремонт. Электродвигатели с фазными роторами более поздних выпусков короткозамыкающих устройств не имеют.
У контактных колец фазных роторов часто повреждаются рабочая поверхность и изоляция между кольцами или между кольцом и валом. Неравномерную выработку контактного кольца устраняют проточкой на токарном станке или при помощи приспособления (см. рис. 116, а).
При легких повреждениях поверхности контактных колец (подгаре, царапинах и других) их шлифуют стеклянной шкуркой или с помощью приспособления (см. рис. 116,5).
Нарушенную изоляцию между контактными кольцами восстанавливают, зачищая, промывая и затем окрашивая поврежденное место изоляционной эмалью ГФ-92ХС или ГФ-92ГС. При предельном износе приходится изготовлять новые кольца и напрессовывать их на вал ротора. Кольца для электрических машин нормального исполнения изготовляют из стали, чугуна или латуни JI68. Существует -несколько способов прессовки контактных колец, но для асинхронных машин мощностью до 100 кВт с фазным ротором чаще других применяют способ холодной прессовки колец на втулку (рис. 124).
Рис. 124. Посадка контактных колец на втулку холодной прессовкой:
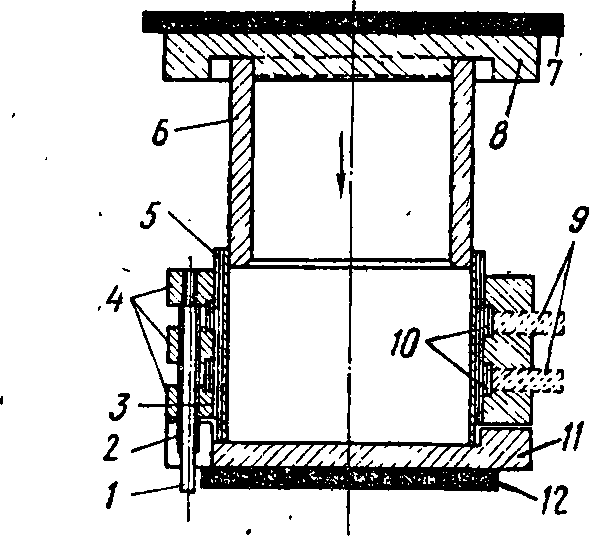
1 и 4 контактные шпилька и кольца, 2 — изоляция контактной шпильки, 3- разрезная стальная гильза, 5 — изоляция стальной разрезной гильзы, б — стальная втулка, 7 и. 12 -верхний и нижний столы пресса, 8 и 11 — верхний и нижний диски, 9 — дистанционные клинья, 10 — электрокартонные прокладки под дистанционными клиньями
Основные операции сборки и прессовки колец выполняют в такой последовательности:
собирают комплект колец, продев контактные шпильки 1 в отверстия колец 4;
вставляют в промежутки между кольцами равномерно по окружности по три стальных дистанционных клина 9, чтобы кольца не смещались при прессовке;
устанавливают комплект колец на нижний (подставной) диск 11 и вкладывают в отверстия колец изоляцию 5, состоящую из полосок пропитанного электрокартона толщиной 0,4 мм и миканита или лакоткани; изоляцию распределяют так, чтобы она равномерно располагалась по внутренней Окружности колец;
вставляют внутрь колец разрезанную гильзу 3 из стали толщиной 1,5 мм, предохраняющую изоляцию от повреждения при прессовке, а затем в эту гильзу — стальную втулку 6 и накрывают ее верхним (нажимным) диском 8;
устанавливают весь собранный комплект колец на нижний стол 12 пресса и запрессовывают втулку б в гильзу 3, после чего выбивают дистанционные клинья из межкольцевых промежутков ;
сушат комплект запрессованных колец в печи в течение 6-8 ч при 110—115 °С, затем пропитывают изоляционным лаком и вновь сушат 10—12 ч при 120°С;
охлаждают комплект колец до 80 — 90 °С и, установив втулку на конец вала ротора, насаживают на вал давлением пресса; при насадке втулки с комплектом колец на вал следят, чтобы контактные шпильки 1 пришлись против выводных концов обмотки;
протачивают поверхности колец на токарном станке, устраняя неровности и биение, затем их шлифуют и полируют;
проверяют индикатором величину биения колец (не должно быть более 0,04 мм).